현대 플라스틱 제조에 있어, 다재 성형(MCM)은 제품 디자인을 다양화시키고, 조립공정을 심플하게 하는데 있어 널리 적용되어 왔다. 이상적으로, MCM은 둘 이상의 재료, 같은 재질의 다른 색 또는 재 사용 재료와 원 재료를 사용하여 제품 생산하기 위한 금형에 주입하는 방법이다. 그 제품은 여러 색상을 결합할 뿐 아니라. 부드러운 표면과 단단한 내부의 조합과 같은 다양한 기능을 할 수 있다. MCM 공정을 실제로 사용할 때는 많은 어려움이 있다. 첫 번째로, 캐비티 교체 메커니즘과 다양한 가소화 단위의 설정을 하는데 있어 선택의 다양함에 있다. 또한, 한가지 재료의 성형에 적용되었던 규칙들이 MCM에 직접 적용 할 수 없다. 마지막으로, MCM 공정으로 사출하는 동안 복잡한 현상과 명확하지 않는 물리적인 메커니즘으로 인해, 기존의 시행착오 방법이 제품 품질의 중요한 요소를 잡을 수 있는 능력에 대한 제한이 있다. [1-8]
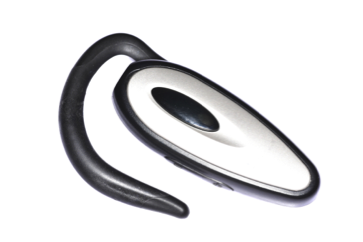
그림 1. 한 제품에 다양한 기능들 : (a) 화장품 패키징에 다양한 색, (b) 장난감에 적용된 인 몰드 조립, (c) 이어폰 후크
이 작업의 방식에 대해 좀더 명확한 이해를 얻기 위해서, 다양화된 MCM 공정을 그림2 에 보여진 것처럼 2 그룹으로 분류 할 수 있다. 첫 번째 그룹은 별개의 인터페이스를 가진 제품을 생산하는 가장 일반적인 과정이다. 이 그룹은 인서트 성형, 오버 몰딩 그리고 sequential multiple shot 몰딩이 있다. 두 번째 그룹은 두 재료 사이의 불확실한 접점을 가지고 있다. 이 불명확한 접점은 제품 설계자에게 큰 문제점을 제기한다. 설계자는 원하는 재료 분배를 하기 위해 정확한 게이트의 위치를 추측해야 한다. 보통 이 작업은 단지 금형 실험을 통해서 하지만 제품의 현상이 복잡하면 제한이 있다. Co-injection 성형 및 Bi-injection 성형이 이 그룹에 속한다. 또한, 이러한 공정들은 주입과 노즐 차단의 일관된 움직임을 필요로 한다. 이는 금형 설계 및 사출기, 배럴 설계를 복잡하게 만든다.
그림 2. 다재 성형 공정은 둘로 나눌 수 있다. (왼쪽) 별개의 계면 시스템, (오른쪽) 불확실한 계면 시스템
따라서, MCM 공정의 복잡한 현상과 명확하지 않는 물리적 메커니즘을 해결하기 위해, CAE 금형 충전 시뮬레이션은 문제 진단 및 설계 검증을 위한 매우 강력한 도구가 될 수 있다. 예를 들어, 터치 패드는 원래 개별적으로 사출된 부품의 조립을 하도록 개발되었다. 이는 적은 변형을 만들지만, 낮은 계면 접착 강도가 제품의 불량을 일으킨다. 오버 몰딩 공정을 사용하여(그림3a), 계면 강도가 향상되었다. 그러나 심각한 변형 문제가 쉽게 발생한다. 그 이유는 두 재료 사이의 계면에 축적되는 열 때문이다(그림3b). 원래의 디자인과 일체형 사출 성형의 공정 조건은 MCM에 직접 적용 할 수 없다. 변형 문제는 제품의 디자인과 다양한 가공조건으로 해결된다[1-4].
a. b.
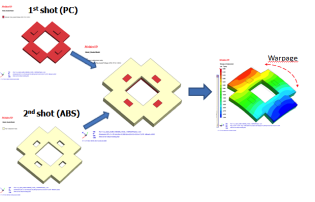
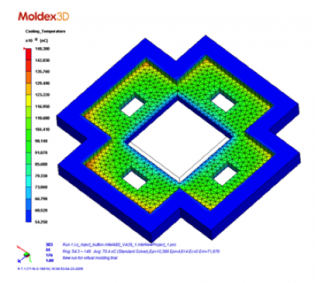
그림 3. 터치 패드는 다재 사출 성형 공법들을 통해 개발된다 : (a) 오버 몰딩 공정으로 이하여 변형 문제를 일르 킨다.(b) 그 변형은 두 재료의 계면을 따라 축적되는 열에 의한 것이다.
또한, Co-injection성형을 사용하여 다르는 표면 재질과 내부 재질로 만든 제품이 많다. 예를 들어 부드러운 촉감의 표면과 단단한 내부, 새 수지를 적용한 표면과 재 사용 수지를 적용한 내부, 일반 표면과 섬유 강화 수지를 적용한 내부 등 있다. 소비자 제품, 자동차 부품 및 구조 강화용 제품들이 Co-injection성형을 사용하여 성형한다. 오늘날 직면한 주요 과제는 캐비티 내부의 재료가 들어가는 공간의 분포를 제어하는 것이다[5-8]. 예를 들어, 그림4 는 이어폰 고리 디자인이다. 고리는 핸드폰과 마이크를 연결한다. 그 디자인은 귀에 착용하고 있는 동안 더 나은 느낌을 제공하기 위해 유연하고 부드러운 표면을 가져야 하고, 변형을 견딜 수 있는 충분한 강도를 가져야 한다. 기존의 기술은 오버 몰딩 공정을 통해 PP를 코어로 하고 TPE를 표면으로 결합한다. Co-injection성형은 단순화된 워크플로우와 재료 사이의 더 나은 접합 강도에 대해 검증되었다. 그러나 실제로는 스킨과 코어 재질의 비율은 불분명하다. 그림5는 CAE 결과를 보여준다. 예측에 따르면, 50%의 스킨 비율은 결함으로 이어지는 코어의 Break-through를 유발할 것이다. 70% 스킨 비율은 더 나은 스킨/코어 비율로 예상되지만, 불행히도 변형 수준이 기능적으로 큰 문제를 일으킨다. 그 시뮬레이션 툴은 그림6 에 보여진 것처럼 게이트의 위치 수정을 제안한다. 한 디자인은 lock영역에서 매우 낮은 코어의 충전을 유발한다. 앞서 언급한 코어의 Break-through현상을 수집하고 분석하면 이 문제를 잘 해결할 것이다. 40%의 스킨 비율을 유지하면서, 0.07초에 Break-through가 발생한다. 그리고 Break-through 이후에, 후크 부분은 사양에 맞는 더 좋은 기계적 강도를 제공할 수 있는 단단한 PP 재료를 사용한다.
a.
b.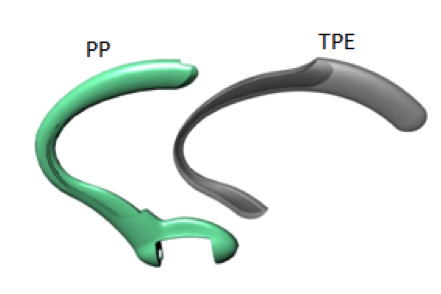
그림 4. 이어폰 후크 : (a) 기하학적 디자인 ; (b) 오버 몰딩 공정으로 코어는 PP로, 스킨은 TPE로 만든다.
그림 5. 이어폰 후크 개발을 위한 CO-injection 몰딩 공정 : 50%의 스킨 비율은 Brea-through가 생긴다.
70%의 스킨 비율은 좋은 스킨/코어 비율이 예상되지만, 변형이 규격에 맞지 않다.
그림 6. CAE는 효과적으로 게이트 위치의 재 배치를 도와준다.
그림 7. (a) 40%의 스킨 비율을 재 검토 : break-through가 0.07초에 발생함 ; (b) Break-through가 생긴 후,
후크 부분은 사양에 맞는 더 나은 기계적 강도를 제공하는 PP재료가 사용되어 진다.
요약
다재 성형(MCM)은 현재의 제품 개발에 널리 적용된다. 그러나, 그것의 복잡한 현상과 명확하지 않는 물리적 메커니즘, 기존의 시행 착오 방법으로는 효과적으로 결정적인 요인을 잡을 수 없다. 오늘날, 오버 몰딩 시스템, Co-injection 몰딩 시스템의 종류에 상관없이 CAE는 최적화된 게이트의 위치를 검증하고 Break-though의 발생 없이 최대치의 코어 비율을 평가하고, 두 재료 사이의 수축과 변형을 평가하는 데에도 매우 유용한 툴을 제공한다.
참고 문헌
1. US patent #3,051,994.
2. Multi-material Technology, Battenfeld.
3. Web source https://www.engelmachinery.com
4. Chao-Tsai Huang et al, SPE ANTEC, 1888-1892 (2006).
5. P.J. Garner and D.F. Oxley, British Patent 1,156,217 (1971).
6. V. Goodship and J.C. Love, Multi-Material Injection Molding (2002).
7. R. Seldén, Polymer Engineering & Science, 40, 1165 (2000).
8. F. Ilinca, J.F. Hetu, and A. Derdouri, International Journal for Numerical Methods in Fluids, 50, 1445 (2006).