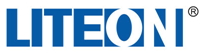
- 고객: Lite-On Technology Corporation
- 국가: 대만
- 산업: 전자
- 솔루션: Moldex3D Advanced
수행 요약
베어링 부시는 베어링 제품에서 중요한 역할을 하는 구성품이다. 마찰 마모를 방지하여 기계수명을 연장시킨다. 플라스틱 사출공정을 통해 베어링 부시 파트의 진원도와 크기가 원 사양에 맞도록 고수하는 것이 관건이었다. 그래서, 치밀한 감독아래 공정이 관리되고 제어될 필요가 있었고, 감독이 미진하면 각 구성품 간 크기가 맞지 않아 기계가 운전 중에 소음이 발생하였다. 또한, 이로 인해 제품의 수율이 크게 하락하였다. 그러나, 정확한 제품사양을 성취하며 성공할 수 있는 핵심 열쇠는 유동단계에서 플라스틱 유동을 여하히 균일하게 하는가에 있었다. 물론, 베어링 부시의 파트 두께를 적절히 유지하면서 말이다. Moldex3D 해석으로, Lite-On Technology사는 적절한 파트두께로 설계하되 최적 게이트위치를 찾아내고 제품의 품질과 수율을 개선하는데 현격한 성공을 이루었다.
해결 과제
- 파트 진원도 불량: 롤링베이어링이 운전 중 진동과 소음 문제를 야기
- 진원도에 대한 엄격한 제품요구사항: 진원도는 0.05mm 이내 제어되어야 함.
해결안
최고의 최적 설계와 제조 조건을 구하기 위하여, Moldex3D 해석이 수행되었고, 수율을 개선할 목적으로 다음과 같은 주요한 과제를 수행 하였음:
1. 핫스폿을 일으키는 원 설계의 문제성 영역을 지정
2. 용융 균형 뿐만 아니라 효과적인 보압효율을 얻기 위해 게이트위치를 변경
3. 불균형 유동과 보압효율 불량으로 기인되는 변위와 변형 감소
4. 원 설계와 생산 상 최고설계로 선택된 여러 최적설계를 비교
5. Z축 방향 진원도 오차를 측정하고자 실린더 영역 내 여러 노드를 배치
연구 사례
원 설계에서 여러 곳에서 다른 두께로 설계되어 바람직하지 못한 성형 문제가 발생했고, 원 설계에서의 게이트 위치는 얇은 벽(1mm)에 위치하고 있었다. 유동단계에서 온도가 낮은 금형벽과 먼저 접촉하게 되어 용융플라스틱이 예상보다 조기에 응고하였다. 이것은 다음단계의 보압 효율에도 악영향을 주었다. 또 다른 문제는 유동경로 말단에 보다 두꺼운 벽(2.2mm) 놓여 있어 파트의 실린더 부인데 두께 때문에 열이 쉽게 축적되고 그 위치의 냉각이 큰 난제가 되었다. 제품을 대기온도까지 냉각하자 이 두꺼운 실린더가 부가 수축과 변형에서 더 큰 부피변형을 명백히 나타내었다. 그러나, 실린더의 진원도에 대한 정밀도는 제품품질 상 합.부를 오락가락 하였다. 따라서, 다음단계인 설계변경과 최적화 단계에서의 주목표는 해당 진원도를 0.05mm 내로 맞추는 것이었다.
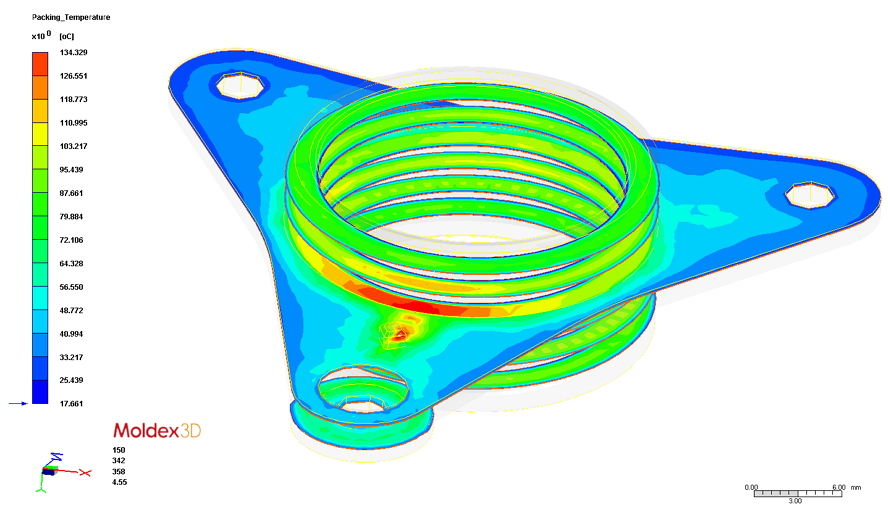
제품 벽두께 변화
실린더형 몸체의 수축문제를 감소시키기 위하여 두 가지 주요 접근방식이 제품설계변경을 고려하여 설정되었음:
1. 원래의 게이트위치를 유지하되, 중앙 실린더 몸체의 두께를 부피변형만큼 잘라내 감소시킴.
2. 해당 영역에 대한 효과적 보압을 보장하고자 성형품의 외곽 원주 상에 게이트를 위치시키도록 변경함.
상기 언급한 바를 기준으로, 5가지 설계변경 옵션이 해석되고 실 시제작으로 검증되었음.
Design 2: 원 게이트 위치 불변. 실린더 몸체까지 경과하는 플라스틱 용액의 양을 감소시켜, 더 균일한 수축값을 얻도록 함. 이로써 실린더 영역의 진원도가 더 안정적이 될 것으로 기대됨.
Design 4: 성형품의 외곽 원주 상에 게이트를 위치시킴. 실린더 몸체에 보압을 충분히 유지시키는 데 도움이 되었음. 반면, 해당 영역의 두께는 감소되지 않아, 전체적인 수축율은 여전히 상당히 높았음.
Design 6: 재료가 코어 측에서 외곽영역까지 감소되었고, 게이트 위치가 플라스틱 용액을 사출하는 캐비티 측으로 이동되었음. 그러나, 실린더 영역 내 불균등 수축의 문제는 여전히 잔존함.
요약하면, 원 설계와 최적 설계들간 전 변위 분석을 비교하여, Design2가 설계변경과 최적화면에 최고의 옵션으로 결론지었다.
원 설계와 최적설계들 간 비교
원 설계와 최적설계간의 전체 변위 비교
제품은 Design 2를 기준으로 재설계되었고, 재측정되었음. 0.05mm보다 작은 직원도로 측정되었고 설계는 사양을 만족시켰음.
진원도는 좌표측정기(CMM)로 측정됨
장점
Moldex3D 수행 전에, Lite-On Technology 사는 베어링부시의 낮은 수율 때문에 이를 대량생산하는 것을 어렵다는 것을 알고 있었다. Moldex3D 해석결과와 실 성형결과의 관계를 분석을 통해, Lite-On Technology는 수율을 거의 99%까지 끌어올리는 데 성공하였다. 이로써 성형시작과 재작업에 드는 비용을 현저히 감소시켰고 시장출시도 단축시킬 수 있었다.
Moldex3D의 진정한 3D 가시화로 제조문제를 눈앞에서 확인하게 된 것이다. 가상 프로토타입과 공정최적화로 제품설계자는 개발프로세스에서 설계변경을 단시간 내 보다 쉽게 성취하게 되었다. Moldex3D로 제품제조에 대한 해결안을 얻은 것 뿐만 아니라 경쟁력있는 장점을 제품에 녹여내는 강점을 제공한 것이다.