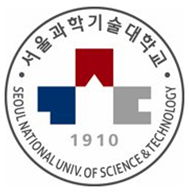
- 고객: 서울과학기술대학교 미케니컬시스템설계 엔지니어링 과
- 국가: 대한민국
- 산업: 아카데미
- 솔루션: Moldex3D Advanced
수행요약
2005년이래, 서울과기대는 Moldex3D 해석결과를 활용하여 기계적 시스템설계의 시험검증을 중점적으로 수행하였고, 학문적 및 산업적 개발 양측면에 상당한 영향을 끼치는 수많은 논문을 출판하였다. 본 연구는 그중의 하나로, 세계적 회사인 LG전자 금형기술센터와 펄스형 금형온도제어를 사용하여 냉각성능을 조사하기 위한 공동개발을 협업한 박 근교수의 논문을 발췌한 것이다.
과제
최근 모든 제조업체는 더 얇고 더 가벼우면 구조강도에도 더 우수한 전자제품을 제조하기 위해 새로운 접근방법에 고군분투하고 있다. 제품품질을 확보하기 위하여 사출성형공정중 웰드라인이나 잔류응력과 같은 잠재적 문제를 방지코자 금형온도를 올려야 한다. 제품파트의 표면품질이 개선되겠지만, 더 높은 금형온도로 냉각시간과 주기시간 역시 상대적으로 증가된다. 따라서, 금형온도를 유지하면서 냉각시간을 더 짧게하는 방법은 효율적이고 비용 효과적인 제조을 고려하는 금형설계자에게는 중요한 이슈이다
솔루션
금형온도의 동적제어가 이러한 이슈를 처리하는 방법으로 채택되었다. 본 연구에서, 펄스형 금형온도제어가 성형단계 전후 온수 및 냉수를 교대로 순환시켜 생산성뿐만 아니라 제품품질을 개선하는데 제안되었다. 냉각단계에서 주기시간에 영향을 끼치지 않고 온도를 빠르게 더 낮출 수 있었다. 가열 및 냉각 효율의 관점에서 전통적인 금형냉각시스템과 해석결과를 비교하였다.
사례
본 연구에서, 서울과기대는 Moldex3D의 정확한 해석능력에 기반하여 금형의 트렌지언트 온도를 조사하였다. 펄스형 금형온도제어 기술을 채택하여 금형표면의 온도결과를 전통적 냉각시스템과 비교하였다. 그림3에서, 전통적 냉각시스템을 사용할 때 전 주기시간은 21초, 각 주기당 온수온도를 60도씨로 연속 주입되었다. 반면, 펄스형 냉각시스템은 80도씨 물로 주입을 시작하여 냉매가 40도씨까지 변화되고, 충진단계의 0.5초 이후 연속으로 11.5초동안 연속 주입되었다. 냉각단계 동안 80도씨 물이 9초 동안 재주입되었다.
그림3. 전통적 냉각법과 펄스형 냉각법과의 냉각시간 비교
Moldex3D의 3차원 트랜지언트 열전달해석 능력으로, 특정시간에서의 온도분포가 정확하게 예측될 수 있었다. 그림4와 그림5는 전통적냉각시스템과 펄스형 냉각시스템과의 금형온도 변화를 보여준다. 펄스형 냉각법으로, 온수 및 냉수가 교대로 순환될 때, 주기시간을 증가시키지 않고 금형온도는 올릴 수 있다.
그림4 전통적 냉각법에 의한 금형온도분포의 변화(℃)
그림5 펄스형 냉각법에의한 금형온도분포의 변화(℃)
그림6(a)은 펄스형 냉각시스템로 성형주기시간을 20초 가량 단축시킬 수 있음을 보여준다. 냉각단계의 최종온도로 비교 시, 펄스형 냉각제어의 최고온도는 전통적 냉각의 온도보다 3.2℃더 높고, 펄스형 냉각제어의 최저온도는 전통적 냉각의 온도보다 7.3℃더 낮다(그림6(b)).
그림6(a) 전 성형주기 그림6(b) 최종 성형주기
결과
Moldex3D의 3차원 트랜지언트 온도분포 결과로, 사용자는 정확하게 바리오썸(variotherm) 기술의 영향을 예측하고 금형 제조단계 이전에 잠재적 문제를 방지할 수 있다. 본 연구에서, 가열 및 냉각 효율을 쉽게 가시화하여 해석결과를 신속한 시험 검증의 효과적방법으로 사용하였다. Moldex3D Advanced 패키지와 추가 모듈을 사용하여 서울과기대는 압축몰딩, 가스주입 사출성형 등 여러 종류의 특수 제조공정에 대한 시험검증도 수행 할 수 있었다. 현재 Moldex3D는 전세계 많은 선도 교육기관에서 교육적 목적 뿐만 아니라 학문적으로나, 경제적으로나 기술적으로 경쟁력을 유지하려는 학생들을 지원하기 위하여 사용되고 있다.
*주: 본 논문은 2012 제조, 기계설계 및 트리볼로지 국제컨퍼런스에 발표되었다.