- 고객: Taiwan University of Science and Technology
- 구역: 대만
- 산업: 교육
- 솔루션: Moldex3D Advanced / DOE Module
수행 요약
캐스팅은 콘택트렌즈를 만드는 가장 일반적인 방법 중 하나이다. 반응 사출 성형 기술은 Front Shell과 Basic Shell을 포함하여 콘택트 렌즈를 제조하는 방법으로 사용된다. 두 개의 shell사이에 사출된 고분자는 응고되어 콘택트 렌즈가 될 것이다. 콘택트 렌즈의 제조 기준이 높은 치수 정밀도를 필요로 하기 때문에, 제품의 변형이 작고 수용 가능한 공차 내에서 제어 되어야 한다. 따라서, NTUST에서 연구진은 Moldex3D의 시뮬레이션 기술로 돌아섰다; 이들은 Moldex3D의 DOE모듈을 사출 공정을 시뮬레이션 하기 위해 활용한다. 그리고 성공적인 변형 개선을 위한 제품 설계 변경을 하기 위해 최적의 공정 조건 설정을 얻을 수 있게 한다.
그림 1. 콘택트 렌즈의 Front shell 과 basic shell
도전과제
- 양산을 위한 다캐비티 제조법을 사용하기에 제한되는 제품의 치수에 대한 제어의 한계.
- 높은 치수정밀도를 요구하는 사출품은 최종 광학 제품을 얻기 위해 이차 가공이 필요하므로 이 공정 단계에서 변형을 최소화 할 필요가 있다.
해결안
Moldex3D DOE 모듈을 활용하면 성공적인 제품 변형 문제 개선을 위한 공정조건 최적화를 얻을 수 있다.
장점
- 교육적인 연구를 진작시키고 NTUST 연구원과 학생들이 CAE 소프트웨어를 사용하여 성형 과정을 시각화 하는 실무 경험을 얻을 수 있게 도움을 준다.
- 인건비의 절감 뿐만 아니라 금형 시험 시간과 위험의 감소.
- 제품의 변형률이 28% 개선되었다.
연구 사례
이 사례는 NTUST 연구원들이 Moldex3D CAE 시뮬레이션 소프트웨어를 사용하여 금형 수정 비용 절약을 위해 가장 중요한 콘택트 렌즈 제조의 공정 조건 접근을 어떻게 평가하고 나타냈는지 설명하는 완벽한 사례이다. 먼저 Moldex3D DOE 모듈은 수축 변화 측정에 사용되었다. 그러면 설계변경을 위한 최적의 변수를 얻을 수 있다. 이에 최종 제품의 품질을 향상 시킬 수 있다. 이 케이스의 주된 목표는 제품 품질에 영향을 주는 품질 계수로, 전 변위와 같은 변형을 줄이는 것이다. 그런 다음, Moldex3D의 DOE 모듈 설정에서 변형 상태에 영향을 미치는 제어 인자로 다른 네 개의 중요한 매개 변수를 선택한다. 그림 2를 보면 제어 인자는 금형 온도, 수지 온도, 보압력, 냉각 시간이다. CAE 실험 설계 방법은 각각의 영향력 있는 인자의 효과를 해석하는 것으로 나타난다. 각 인자의 직접적인 영향은 그림3 Factor response plot에 도시 되어있다. 그림3에서 제어인자B(용융온도)는 가장 중요한 인자로 나타내고 있다.
그림 2. Moldex3D DOE 모듈의 제어 인자
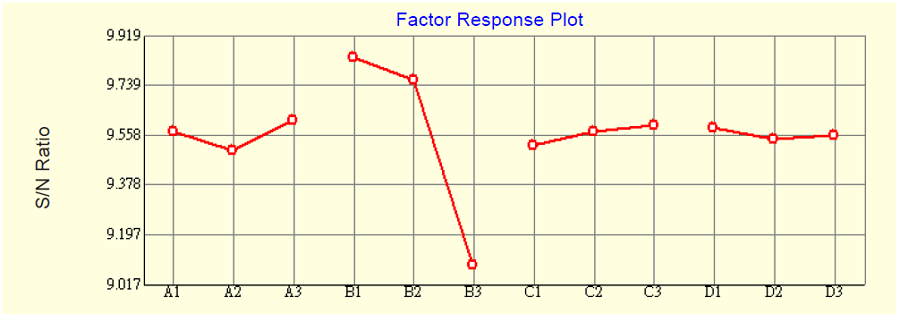
그림 3. Factor response plot
추가로, Moldex3D의 해석을 따르면(그림4) 초기 설계에서는 불균형 유동이 발견되었다. 제품이 80%충전 되었을 때, Basic shell은 완충되었고, Front shell은 아직 절반 밖에 차지 않았다. 이러한 결과 때문에, Front shell의 게이트 크기 넓혀 빠른 충전을 유도하였다(그림5). 설계가 변경 됨에 따라 다시 Moldex3D 시뮬레이션을 통한 성능 테스트를 하였다. 그림6에서 유동 밸런스가 상당히 개선된 것을 볼 수 있다. 이 케이스는 교육적인 목적을 가지고 학생들에게 성형 이슈의 예측과 개선을 위한 CAE 시뮬레이션 툴 사용의 이해를 돕는 방법으로 접근하였다. 몇 가지 추가적인 설계 변경이 시험 및 구현된 경우, 충전 성능을 개선하는 것은 더 중요할 수 있다.
그림 4. 초기 설계
그림 5. 설계 변경
그림 6. 설계 변경 후의 유동 선단
다음 표(표1)은 초기 설계, DOE(최적) 및 설계 변경의 시뮬레이션 결과를 나타낸다. Moldex3D의 DOE 모듈의 도움과 설계 변경의 효과를 통해, 총 개선율은 17.28%에 도달 할 것으로 예측 된다. 따라서 변위 문제가 크게 개선 될 것이다(그림 7).
표 1. 비교표
그림 7. 변형 변화
결론
Moldex3D의 DOE 모듈은 NTUST연구원들의 성형과정의 시각화와 효과적인 공정조건 설정을 위해 제품 품질에 영향을 주는 중요한 영향 인자가 무엇인지 나타내는 것을 돕는다. 또한 NTUST의 연구원과 학생들에게 Moldex3D는 실제 현장의 경험을 얻을 수 있는 실습 기회를 주고, 산업현장에서 경험을 쌓기 전에 효과적으로 제조 위험을 줄이고 시행착오를 피하기 위해 CAE 시뮬레이션 소프트웨어를 사용 하는 방법의 교육을 제공한다.