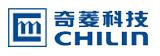
(출처: https://www.chilintech.com.tw)
최근 수년간 Chi Lin은 정밀 사출 성형 산업으로 사업을 확장했다. Chi Mei는 이를 통해 TFT-LCD 시장의 주요 부품을 포함하여 광범위한 플라스틱 제품을 생산할 수 있게 되었다. 다양한TFT-LCD 제품 요구 사항을 만족시키려면 플라스틱 제품의 형상은 매우 복잡해질 수 있다. 게다가, 생산 비용과 효율성 문제는 금형 개발과 설계를 더욱 어렵게 만든다. 오늘날 TFT-LCD 제품을 개발할 때 기본적으로 요구되는 사항은 경량화, 슬림화 및 대형화이다. 이러한 기준을 만족시키는 것은 언제나 커다란 도전이다. 2002년 Chi Lin는 Moldex3D 시뮬레이션 해석 기법을 채택하여 제품의 초기 설계 단계에서 제품 설계의 실현 가능성을 가늠해보았다.
Moldex3D로 최초 디자인의 결점 발견
이번 논의에서는 TFT-LCD 플라스틱 기판을 예로 들어 설명한다. TFT-LCD 플라스틱 기판은 1.5 mm 미만의 평탄도(flatness)가 요구되며 플래시 및 먼지 문제가 허용되지 않는다. 이러한 요구 조건을 만족시키기 위해서는 디자인 측면에서 두 가지 문제를 고려해야 한다: 높은 사출 압력은 잔류 응력을 높여 휨 문제를 야기하고, 불충분한 형체력은 플래시를 유발한다.
(1) 정체 현상
이 제품 개발에 대한 좀 더 정확한 이해를 위해 미성형 검사를 통해 충진 행태를 수치적으로, 실험적으로 측정하였다. (그림1, 3)은 시뮬레이션 결과를 보여주고 (그림2, 4)는 최초 디자인의 실험 결과를 보여준다. 이 두 사례를 통해 수치적 예측과 실험 검증이 일치하는 것을 알 수 있다. 이 결과를 통해 부품의 중심 부분에 정체가 발생한 것도 알 수 있다. 이 그림들은 유동 선단의 분포와 웰드 라인의 위치도 보여준다. 또한, 유동 선단의 성장을 통해 캐비티의 충진 상태를 항상 관찰할 수 있으며, 웰드 라인과 에어 트랩의 위치도 예측할 수 있다. 사용자는 미성형 현상을 측정하여 공기 배출구를 설치해야 하는 위치를 식별해낼 수도 있다.
![]() |
![]() |
![]() |
그림1 최초
|
그림2 최초
|
그림3 최초
|
![]() |
![]() |
|
그림4 최초
|
그림5 최초
|
(2) 너무 높은 형체력
스프루 압력과 형체력의 시간에 따른 변화 곡선(그림6, 그림7)에서 스프루 압력은 최대 114MPA(1 MPa=9.8kg/cm2)이고 형체력은 1200톤까지 올라간다. 이러한 변화 곡선을 통해 충진/보압 단계의 압력 거동과 요구되는 형체력을 모니터링할 수 있으며, 이를 통해 러너와 게이트의 압력을 결정할 수 있다. 따라서, 사용자는 러너와 금형을 디자인할 때 이러한 측정된 압력을 참고할 수 있다.
![]() |
![]() |
그림6 스프루 압력의 시간에 따른 변화 곡선 |
그림7 형체력의 시간에 따른 변화 곡선 |
(3) 너무 높은 응력
최초 디자인의 전단 응력 분포(그림8)는 높은 응력(>1Mpa)이 제품 휨 현상의 주요인이라는 사실을 입증한다. 일반적으로 응력은 0.5 MPa(1 MPa=9.8kg/cm2) 보다 높아서는 안 된다.
그림8 전단 응력 분포
(4) 심각한 휨 문제
축의 휨 변위는 –1.46~1.56 mm 사이에 분포한다(그림9). 이 결과는 휨이 매우 심각하며 기준에 맞지 않는다는 것을 보여준다.
그림9 두께(Z축)의 휨 예측
문제의 정확한 해결로 최종 제품 개선
최초 디자인의 주요 문제는 부품에 두 곳의 얇은 부분이 존재한다는 점이다. 수정된 디자인은 이 두 곳의 두께를 증가함으로써 최초 디자인의 문제를 해결하고 있다.
(1) 정체 현상 해결
유동 선단과 실제 금형 샘플(그림10~14)은 정체 현상이 해결되었음을 여실히 보여준다.
![]() |
![]() |
![]() |
그림10 수정된
|
그림11 수정된
|
그림12 수정된
|
![]() |
![]() |
|
그림13 수정된
|
그림14 수정된
|
(2) 스프루 압력 및 형체력 감소
아래 도표에서 보듯이 응력은 89MPA(1 MPa=9.8kg/cm2)로 감소되었으며 요구되는 형체력은 920톤으로 낮아졌다(그림15, 그림16).
![]() |
![]() |
그림15 수정된 디자인: 스프루 압력의시간에 따른 변화 곡선 |
그림16 수정된 디자인: 형체력의시간에 따른 변화 곡선 |
(3) 응력 감소
수정된 디자인의 전단 응력 분포(그림17)에서 보듯 전체 부분에서 전단 응력은 0.5 MPa 보다 작다. 최초 디자인에서 높았던 전단 응력 부분이 제거된 것을 볼 수 있다.
그림17 수정된 디자인의 전단 응력 분포
(4) 휨 문제 개선
마지막으로, 두께의 휨 분포(그림18)에서 휨 정도는 –0.52 ~ 0.56 mm 사이로 제어되었다. 휨 문제가 크게 개선된 것을 볼 수 있다.
![]() |
![]() |
그림18 두깨(Z축)의 휨 분포 |
최초 디자인(상)과 수정된 디자인(하) |
시간과 비용 절감
Moldex3D를 사용하여 사출 제품의 디자인 및 개발에 대한 수치적 시뮬레이션을 수행함으로써 Chi Lin은 중요한 문제를 적시에 해결하여 생산 비용을 절감하고 성능을 향상시킬 수 있었다. Chi Lin Technology Co.의 Lee 사장은, “지난 몇 년간 TFT-LCD 모니터 시장의 경쟁은 매우 치열해졌으며, 따라서 제품의 제조 비용 절감과 제작 라인의 속도 및 효율성 향상은 모든 제조업체에 매우 중요한 문제가 되었다. Moldex3D 시뮬레이션 해석 기술은 이러한 요구를 만족시킬 수 있다. Chi Lin은 2002년부터 Moldex3D 소프트웨어를 사용하여 수백만 개 이상의 제품을 성공적으로 개발하였으며, Moldex3D의 사용으로 연구 개발 비용의 절감 효과뿐만 아니라 R&D 시간과 제품 품질의 향상도 실현할 수 있었다”고 밝혔다.
*CHIMEI Group 정보: 1959년에 창립된 Chi-Mei Corporation은 40년 이상 석유 화학 업계를 주도하고 있다. Chi Mei는 대만 최초의 아크릴 시트 제조업체이다. Chi-Mei가 생산하는 ACRYPOLYR는 대만의 아크릴 시트라고 불리고, Hsu 회장은 “대만 아크릴의 아버지”로 알려져 있다. 2006년 Chi-Mei Corporation의 계열사 총 매출은 US 105억 달러를 넘었으며 총 직원 수는 36,000여명이다.
* 이 사례는 2006년 11월 Moldex3D News No. 15에 게재되었음