- 고객 : BASF
- 국가 : 독일
- 산업 : 소비성 제픔
- 솔루션 : Moldex3D Advanced 솔루션, 유동 분석 모듈, 보압 분석 모듈, 변형 분석 모듈, 가스 보조 사출 성형 모듈, FEA 인터페이스 기능 모듈
총 122,000명의 직원을 두고 있는 BASF는 전세계 산업 거의 모든 분야에 기여하는 기업이다. BASF의 생산 포트폴리오는 화학, 재료, 산업 솔루션, 표면 처리 기술, 영양 보건, 농업 솔루션 등 6대 범주로 구성되어 있다. (출처: https://www.basf.com/global/en/who-we-are.html)
개요
이번 사례의 제품은 BASF섬유 강화 플라스틱 재료를 사용해 가스 사출 성형 기법으로 제작된 디자이너 의자인데, 생산 과정 중 가스 핑거링 문제가 발생해 제품의 강도가 약화되었다. 의자가 디자이너의 작품이기 때문에 설계를 변경할 수 없었던 BASF엔지니어는 공정조건 최적화를 통해서만 제품 강도 및 경량화 요구사항을 고려하면서 가스 보조 성형으로 인한 문제를 해결해야 했다.
문제점
- 가스 핑거링
- 약한 기계적 성질
- 변경할 수 없는 설계
솔루션
BASF엔지니어는 Moldex3D를 이용해 공정조건를 최적화하여 가스 핑거링을 개선했다. 새로운 공정조건으로 생산된 의자가 요구되는 하중을 충족할 수 있는지 테스트하기 위해, 엔지니어는 Moldex3D를 통해 가스 배출 위치, 왜곡 형상 및 섬유 배향이 포함된 중요한 성형 시뮬레이션 데이터를 획득하여 FEM시뮬레이션의 정확도를 향상시켰다. Abaqus에서 FEM 분석을 수행한 결과, 새로운 프로세스 매개변수가 규정된 하중을 충족시키는 의자를 만들 수 있고, 제품의 경량화 요구을 충족하는 동시에 구조의 완벽성도 갖추었음이 드러났다.
효과
- 가스 핑거링 예측
- 제품 강도 60% 개선
- 제품 중량 및 하중 요구사항 충족
사례 연구
본 사례에서 BASF는 Moldex3D를 사용해 가스 보조 성형으로 만들어진 디자이너 의자를 시뮬레이션했다. BASF가 직면한 과제는 의자 표면과 등받이에 발생한 가스 핑거링 현상이며, 이 문제는 하중을 받으면 구조적 손상을 일으킬 수 있다. 디자이너의 작품인 제품은 금형이 이미 제조되어 설계를 변경할 수 없었기 때문에, 공정 조건 최적화를 통해 의자가 요구되는 스펙을 맞추었다.
원래 설계의 분석 결과는 가스 주입 시 제품 두께 사이의 중심점 온도 차이가 2°C 미만임을 보여준다 (그림 1). 즉, 두껍고 얇은 두께 사이의 유동 저항력이 비슷하기 때문에, 가스가 얇은 영역으로 진입하기 쉽다(가스 핑거링 유발). 마찬가지 원리로 두 개 영역의 온도 차이가 비교적 크면 가스는 얇은 영역으로 진입하지 않는다. 따라서 가스 지연 및 충전, 보압시간을 늘리면 공정조건 최적화에 도움이 된다.
그림 1 중심점 온도의 시뮬레이션 결과
BASF는 충전시간을 6초까지, 보압시간을 10초까지, 가스 지연시간을 15초까지 늘리는 등의 다양한 조합을 통해 공정조건 최적화를 시도하였다. 그림 2는 매개변수를 최적화한 시뮬레이션 결과로서 가스 배출을 허용된 영역으로 제한시키는 데 성공했다.
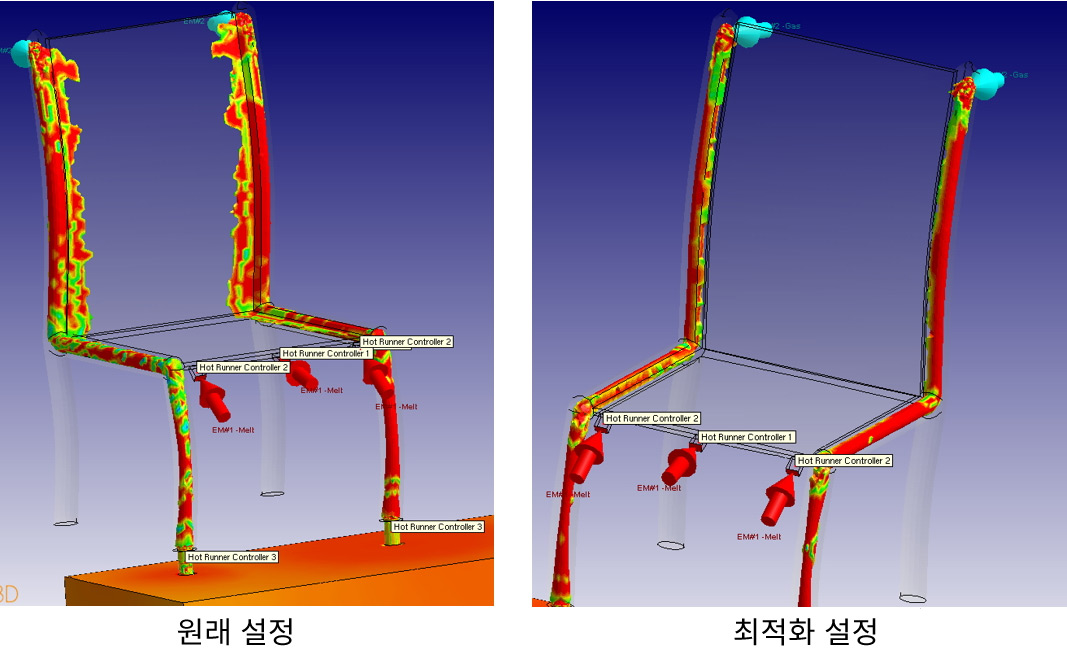
그림 2 매개변수 최적화 전후의 가스 배출 시뮬레이션 결과
설정을 최적화하면 두께가 두껍고 얇은 영역의 중심점 온도 차이가 7~10°C로 변경된다 (그림 3). 이는 가스가 얇은 영역으로 진입하지 않고, 더 높은(두꺼운) 영역으로 흐르기 때문에, 영역이 더 낮은 유동 저항을 갖는 것을 의미하는 것이다.
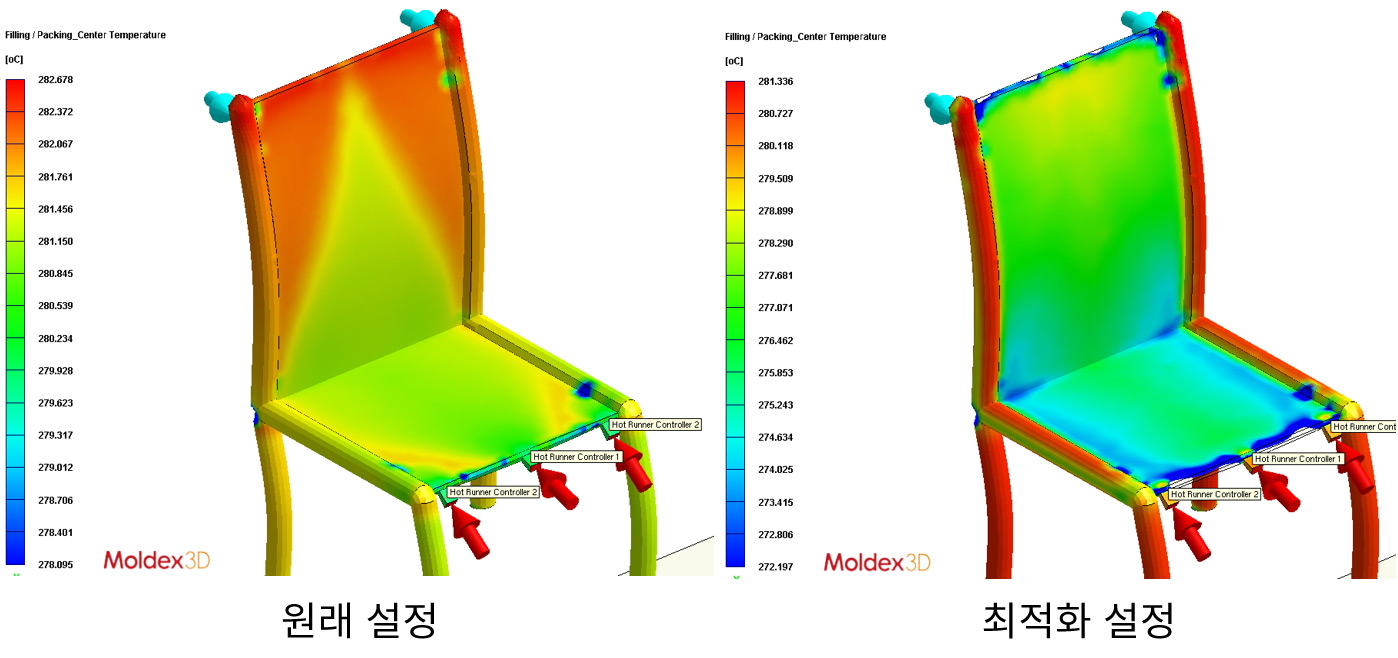
그림 3 원래 설정과 최적화 설정 후의 중심점 온도 차이
Moldex3D는 구조 해석 시뮬레이션을 진행할 수 있도록 시뮬레이션 결과를 유한 요소법(FEM) 분석 소프트웨어로 내보내기를 지원한다. 이번 사례에서 BASF는 Moldex3D 시뮬레이션 결과를 통해 원래 설정 조건 하에서 만들어진 의자를 구조 해석 소프트웨어 Abaqus로 내보낸 결과, 요구사항을 충족하지 않음을 검증했다. 그림 4는 의자에 구조가 손상될 때까지 힘을 가한 상황을 보여주며, 결과는 설정을 최적화하면 원래 설정보다 60% 더 많은 힘을 견딜 수 있음을 나타낸다. 또한, 최적화 설정된 의자는 하중을 받은 후의 변형도 원래 설정보다 11.5% 개선되었다.
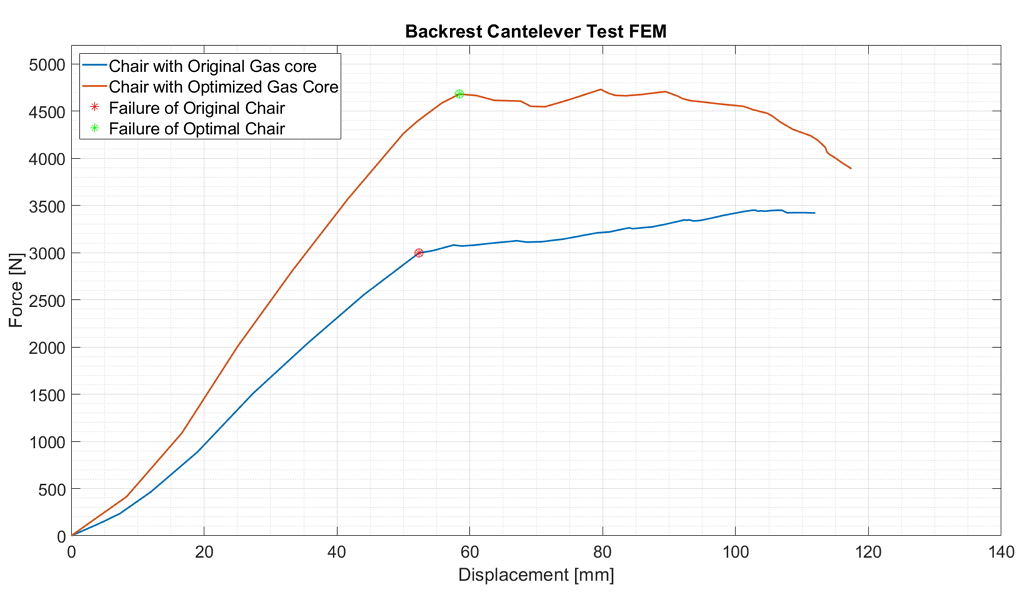
그림 4 Abaqus로 진행하는 제품의 변위와 힘 비교
결과
Moldex3D를 사용하면 가스 사출 성형 기법을 간편하게 시뮬레이션하고, 최적화 결과도 도출 해낼 수 있으며, 그 중 중심 온도의 시뮬레이션은 가스 보조 프로세스에 매우 실용적이다. 또한 Moldex3D FEA인터페이스를 통해서도 후속 FEM분석 프로세스에 필요한 데이터를 얻는데 도움이 됨에 따라, 다른 구조 해석 소프트웨어에서도 내보내진 데이터를 쉽게 읽고 처리할 수 있게 되었다.