사출 압축 성형(ICM)은 정밀 광학 렌즈, 반사경, 저장 매체 등의 제작에 광범위하게 사용된다. ICM 공정은 사출하는 동안 캐비티 간격의 조절된 편차를 이용한다. ICM과 기존의 사출 성형의 가장 큰 차이점은 용융 수지가 캐비티를 채워갈 때 걸리는 압력 프로파일이다. 그림1은 일반적인 사출 성형 프로세스로, 용융체의 압력이 스프루로부터 용융선단까지 모든 방향으로 전달되어야 한다. 이 때, 중심부에는 높은 압력이 걸리고 테두리 부분에는 낮은 압력이 걸리게 된다. 변형이나, 높은 잔류 응력 및 높은 충진압과 같은 성형 불량 및 난점이 이러한 고르지 못한 압력 프로파일 때문에 종종 발생된다. 상대적으로, 그림 2의 ICM 공정은 균일한 압력 분포를 나타내며, 압력 차이가 최소화된다. 따라서 충진압과 잔류응력이 낮아지게 된다.
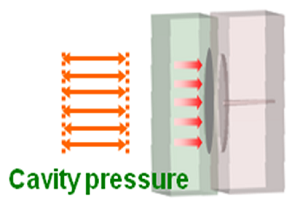
그림. 1 일반적인 사출 성형에서의 불균일한 압력 분포 그림. 2 사출 압축 성형에서의 균일한 압력 분포
광학제품이나 살두께가 얇은 제품처럼 잔류 응력의 문제에 민감한 제품의 경우 ICM 공정을 통해 많은 이익을 볼 수 있다. 그림 3에서 LGP(Light guide plate)의 예를 통해 가해지는 응력을 비교해 볼 수 있다. 응력이 48MPa에서 12MPa로 명백히 줄어드는 것을 비교할 수 있다. 이 외에도 ICM을 적용함으로써 변형을 줄일 수 있고, 공정 시간을 단축시키고, 형체력을 줄일 수 있고, 더 나은 벤팅을 통해 제품 품질을 향상시킬 수 있다.
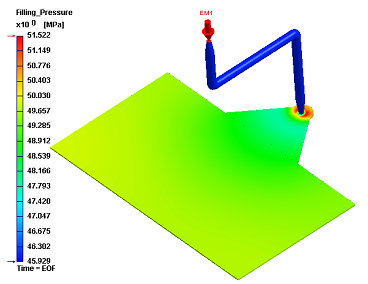
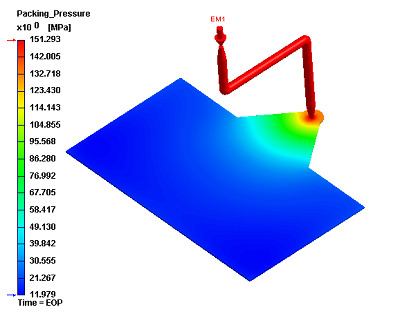
그림. 3 LGP(light guide plate) 제품에서의 일반 사출 공정과 ICM공정의 압력 분포 차이
많은 장점이 있기는 하지만, 사출/압축 타이밍 시퀀스 및 형 이동 조절이 복잡하기 때문에 ICM 공정을 성공적으로 설정하기가 쉽지는 않다. 공정 기술자들은 위에 언급한 한계를 해결하기 위해 시행착오를 통해 적용하곤 했다. 일반적으로 갭 크기와 형 이동은 적절한 사출율 프로파일을 얻기 위해 최우선적으로 정해져야 한다. 전체 공정을 최적화하는 작업은 시간 소모적일 수밖에 없다. 예를 들어, 플래쉬나 미성형이 생기지 않는 초기 조건을 찾기 위해 몇 일이 걸리기도 한다. ICM 공정에서는 자유로운 공정 조건 자체가 버거운 일이 된다.
Moldex3D는 다음과 같은 기능으로 가상의 성형 시험의 완벽한 솔루션을 제공한다.
- 독립적인 금형 부분과 사출기 부분의 동시 또는 순차적인 작동의 동적 계산
- 사출과 압축 속도 프로파일과 압력 조절의 완벽한 설정; 사출 on/off 전환
- 공정 최적화 가이드를 위한 잔류 응력, 보압, 냉각 온도와 같은 후공정 정보를 시각화
- 실제 수축과 평탄도 예측을 위한 섬유 배향 해석을 포함
- 스프루 압력과 형체력과 같은 사출기 관련 정보 평가
광학제품 제조사를 위해, Moldex3D는 광학 모듈을 제공하고 있고, 이는 점탄성 물성에 기초한 독창적인 복굴절 시뮬레이션 도구이다. 이제, 렌즈 제조사는 임의의 입사광 방향 및 파장에 따른 복굴절 패턴을 예측함으로써 잔류 응력을 줄이는 공정 설정을 최적화할 수 있다. 그림 4는 실제 제품과 Moldex3D 해석 결과의 일관성을 보여주고 있다. 광학 제품 제조사는 Moldex3D를 통해 완벽한 성형 시뮬레이션을 할 수 있다. Moldex3D의 신속한 가상 성형 시행은 사출 압축 공정을 최대한 활용할 수 있도록 할 수 있다.
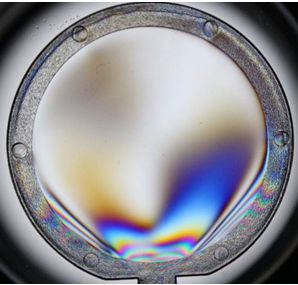
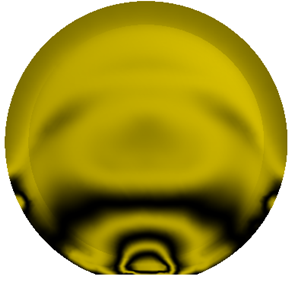
그림.4 성형된 광학 렌즈 제품(왼쪽)과 Moldex3D의 시뮬레이션 결과(우측)의 복굴절 패턴 비교
Related articles:
- A Novel Approach for Predicting Birefringence of Optical Parts
- Simulation and Verification of True 3D Optical Parts by Injection Molding Process