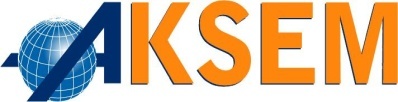
- 고객: AKSEM Plastik Metal Kalip San. ve Tic. Ltd.Sti.
- 국가: 터키
- 산업: 자동차
- 솔루션: Moldex3D eDesign
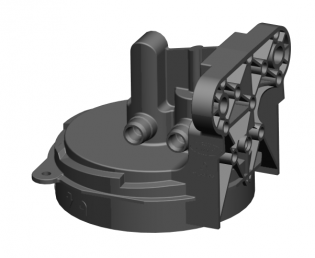
본 사례는 자동차 부품인 오일필터헤드임. 부품의 안전요구사항으로, 변형과 치수오차에 대한 공차가 매우 작은 특성이 있음.
수행 요약
본 사례는 자동차의 오일필터 부품으로서, 제품에 대한 안전요구사항으로 변형과 치수에 대한 공차가 매우 엄격하다. 우선, 플라스틱 성헝(PIM)공정으로 제조된 부품은 자동차 분야에서 널리 사용되어 왔고, 물리적 무게의 감소로 제조비를 감소시키는데 기여하여 왔다. 금형생산에서 수축율은 중요한 설계변수이다. 그러나, 허용범위내 수축율 유지는 특정한 부품의 경우, 특히 실린더 부품과 같이 치수공차에 민감하고 작은 부품일 경우 매우 어렵다. 따라서, 금형의 충진해석으로 문제성 있는 수축영역을 규명하고, 합리적인 범위 내 수축율을 유지하는 것은 기본적인 과제가 된다. 두번째로, Moldex3D 해석을 활용하여, 실 금형의 설계와 구조에 대하여 가치있는 정보를 제공하는 것이 또한 중요하다. 전통적인 시행착오법을 적용하는 것보다 시간과 비용절약 측면에서 훨씬 경제적 접근이 된다는 것은 증명되고 있다. 더구나, Moldex3D DOE(실험계획법) 모듈의 도움으로, 공정단계에 가장 큰 영향을 주는 제조 파라미터를 집어내었을 뿐만 아니라 가장 최적화된 제조 파라미터의 세트도 소프트웨어의 도움으로 쉽게 계산될 수 있었다.
해결 과제
실린더 영역에서 타원형 변위, 평평도 및 냉간 웰드라인 등은 고려해야 할 3대 주요요소이었다. 불균일 수축이 잠재적 오일 누유 문제를 야기시키므로, 향후의 오일누유를 배제하기 위해서라도, 타원형 변형과 언급한 다른 제품결함은 필히 해결되어야 하는 문제이었다. 그러나, 잠재적 성형문제를 효과적으로 직시하고 금형 캐비티 내 성형유동을 가시화하는 것은 하나의 큰 도전이었다. 그러므로, 본 사례의 주 목표는 제품품질을 보장하고 여러 차례 불필요한 금형시작을 최소화하는 적절한 해를 구하는 것이었다.
해결안
더 우수한 제품품질을 얻을 목표를 성취하기 위하여, Moldex3D DOE (실험설계법) 기술을 적용하여 가장 최적화된 제조 파라미터를 생산 전에 규명하였다. 실 금형시작을 통해서, Moldex3D 해석결과가 실 시작품의 결과와 매우 근접한 상관관계를 나타냄을 증명하였다. 즉, Moldex3D 해의 해석을 근간으로, ASKEM은 성공적으로 허용변위 값을 규명하고 관리하였고, 궁극적으로 상당한 시간 절약과 전체적 생산비를 절감토록 이끄는 제품의 평평도를 제어할 수 있었다.
Moldex3D DOE Expert 로 가장 최적 파라미터값을 규명함.
연구 사례
무엇보다도, 본 사례의 가장 주요과제는 최종 제품의 실 치수값을 구하는 것이었다. 이 데이터는 Moldex3D 자체와 DOE모듈을 해석결과를 분석하여 얻을 수 있었다. 치수결과를 알게 되니, 잠재적 수축문제를 찾아낼 수 있었고, 해당 수축율을 교정하고 제품의 오차를 교정하기 위하여, 금형치수 설계에서 상응하는 수정을 실시하였다. 다시 말하면, 제품의 실린더 영역 내 타원형 변위가 Moldex3D 해석에 근거하여 상응하는 금형을 가공하여 상당히 교정되고 개선되었다.
(좌) 변형_전체 변위: 0.102mm~1.53mm
금형설계단계 중 Moldex3D의 변형데이터를 근거로 강과 부품데이터가 수정됨.
둘째로, 또 다른 주요과제는 변형을 감소시키고 제품상 냉간 웰드라인 문제를 감소시키기 위하여 금형설계에서 에어벤팅을 위한 최적 위치를 결정하는 일이었다. Moldex3D해석을 기반으로, 가능한 에어트랩 위치를 먼저 가시화하여 확인하고, 잠재적 에어트랩 문제를 배제하고 발생빈도를 낮추도록 벤팅 레이아웃 설계를 수정하였다. 에어벤팅 레이아웃 설계가 나아지자, 최종 제품의 평평도 또한 개선되고 검증되었다. 냉간 웰드라인 문제도 관리범위 내로 들어오고, 그러한 위치 유지로 향후 오일 누유의 위험도도 줄였다.
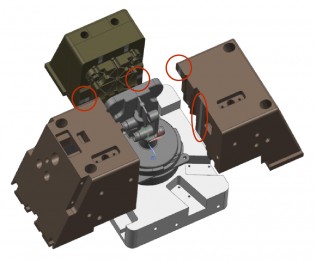
Moldex3D해석을 기반으로, 가능한 에어트랩 위치를 먼저 가시화하여 확인하고,
잠재적 에어트랩 문제를 배제하고 발생빈도를 낮추도록 벤팅 레이아웃 설계를 수정하였다.
더구나, 본 사례에서, 플라스틱 오일필터 헤드 부품은 상대품과 조립되게 되어 있어, 부품 정밀도가 매우 중요하다. 그러므로, 여러 점에서의 점검과 모든 잠재적 문제에 확신을 갖는 작업은 금형의 제조시작 전에 고려되어야 하였고, 그렇게 함으로써, 불필요한 생산비를 피하고 제조리드타임을 단축시키는 것은 매우 중요하였다.
요약하면, Moldex3D 해석을 사용하여, ASKEN 은 문제성 영역을 미리 예측하였을 뿐 아니라 잠재적 문제를 축출하고 금형 제조 전에 상응하는 교정을 수행할 수 있도록 주요 공정 파라미터를 결정할 수 있었다. 나아가, Moldex3D DOE 모듈의 도움으로, 가장 최적화된 공정파라미터가 소프트웨어로 미리 예측될 수 있었고, 엔지니어는 전체 시간을 더 빠르게 수행하고 고품질 최종제품을 생산토록 하는 가치 있는 정보를 예측하게 되었다.
장점
Moldex3D 해석은 양질의 금형설계에 유용한 통찰력을 제공한다. Moldex3D 해석결과를 실 금형시작의 결과와 비교하여, Moldex3D가 단호히 신뢰성 있는 해석데이터를 사용자에게 제공함이 증명되었다. 더 중요한 것은, 제품품질과 생산성을 개선하고자 하는 목표가 성공적으로 수행되었고, 전체적인 생산비가 정확한 해석의 도움으로 감소되었다. 본 사례를 마치면서, Moldex3D는 고능력 플라스틱 사출성형 해석을 성공적으로 수행한다는 것이다. 또한 Moldex3D는 제품설계 단계와 금형제조 단계간 설계 최적화와 검증을 위한 믿을 만한 소스가 되는 가능한 플랫폼을 제공한다는 것이다.