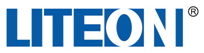
- 고객사:라이트온 테크롤로지(LiteOn Technology)
- 국가:대만
- 산업:전자
- 솔루션: Moldex3D Advanced / FEA 인터페이스 기능 모듈
개요
CIS(밀착형 이미지 센서, Contact Image Sensor)는 스캐너 구조의 중요한 부품 중 하나이다. 라이트온 테크놀로지는 CIS 홀더를 유리와 조립한 이후의 제품 운송과정에서 잔류 응력의 영향으로 CIS 홀더의 변형이 발생하고 나아가 유리와 분리되는 문제가 나타날 수 있음을 발견했다. 이 문제를 해결하기 위해 라이트온 테크놀로지는 Moldex3D Advanced솔루션과 FEA인터페이스 모듈, 구조분석 소프트웨어 LS-DYNA를 통해 제조공정에서 잔류 응력이 제품 변형에 영향을 준다는 것을 찾아냈다. 사출공정 개선 이후 라이트온 테크놀로지는 예정 기간 내에 무결점 제품을 성공적으로 제작했다.
도전
- 긴 제품은 유동 불균형 현상을 초래
- 변형 범위는 반드시 수평방향 0.4mm이내, 수직방향 0.8mm 이내로 제어
- CIS 홀더 변형은 제품 분리현상 초래
해결방안
Moldex3D FEA 인터페이스 기능과 LS-DYNA의 결합을 통해 라이트온 테크놀로지는 별도의 금형 테스트 비용 지출 없이 게이트 위치 및 성형조건 최적화를 완성하고 제품의 휨 현상을 저감하였다.
이점
- 유동 불균형 문제 해결
- X축 변형량 50% 감소(0.34mm에서 0.17mm로 감소)
- 제품 분리 문제 해결
- 제품 품질의 고정밀도 실현
연구 사례
스캐너의 CIS 홀더는 통상 고정밀도를 요한다. 이를 위해 라이트온 테크놀로지는 Moldex3D와 LS-DYNA를 결합하여 CIS 홀더의 사이즈 안정 문제를 개선하고 성형 후의 제품 변형을 허용범위 내로 확보하였다.
그림1. 스캐너CIS홀더(빨간색 테두리)
라이트온 테크놀로지는 Moldex3D Advanced 솔루션으로 제품 오리지널 디자인에 대해 기존 사출 공정 성형 조건의 시뮬레이션을 진행하였다. 그 결과 국부적인 유동 불균형과 부피 수축의 문제가 나타났으며 변형 리스크도 발견되었다. 99.9%까지 충전된 상황에서 충전되지 않은 구역의 충전시간은 충전된 구역보다 0.7초(그림2) 늦었다. 오리지널 디자인의 게이트 수량으로 인해 압력이 게이트 근처로 집중되어 부피 수축률이 지나치게 높아졌다(그림3). 냉각 단계에서, 수축이 높은 구역에서는 기공 또는 움푹 패임 현상이 나타날 수 있다. 본 사례의 제품은 외관 정밀도에 대한 요구치가 매우 높기 때문에 휨 변형은 시급히 해결해야 하는 문제로 꼽힌다.
그림2. 99.9% 충전 시 유동 선단
그림3. 오리지널 디자인 단면의 부피 수축 상황
유동 불균형을 최소화하고 휨 현상을 개선하기 위해 라이트온 테크놀로지는 게이트 디자인을 변경하고, 중앙의 게이트를 제거하고(그림4), 바깥쪽의 게이트 역시 바깥으로 40mm 이동시켰다. Moldex3D의 시뮬레이션 결과에 따라(그림5), 변경 후의 디자인은 휨 변이 현상을 효과적으로 개선할 수 있다.
그림4. 디자인 변형 모형
그림5. 디자인 변경 후의X축 변형
이어 라이트온 테크놀로지는 실험을 통해 시뮬레이션 결과를 검증했다. 그림6에서 보듯 시뮬레이션 분석과 실험결과는 모두 오리지널 디자인에 분명한 변형이 있음을 나타낸다. 이와 반대로 디자인 변경 후의 제품(그림7)에서는 분명한 수축 구역이 나타나지 않았으며 휨 문제도 대폭 개선되었다. 실험을 통해 Moldex3D의 시뮬레이션 결과와 실제 금형 테스트가 일치함을 증명했다.
그림6. 오리지널 디자인의 실제 금형 테스트(좌)와 시뮬레이션 결과(우) 제품 변형 상황 비교
그림7. 디자인 변경 후의 실제 금형 테스트(좌)와 시뮬레이션 결과(우) 제품 변형 상황 비교
Moldex3D는 해석 결과를 구조 분석 소프트웨어에서 불러오고 구조 분석을 수행할 수 있다. 라이트온 테크놀로지는 LS-DYNA를 통해 구조분석을 수행하며 선형탄성 분석 조립 과정이 야기한 변형과 잔류 응력을 보여준다(그림8). 오리지널 디자인에서 CIS 홀더 변형은 유리 구조에 압축력을 가해 유리 분리를 초래할 수 있다. 디자인 최적화 후 약 75%의 잔류 응력을 감소할 수 있다.
그림8. 유리 구조와 CIS 홀드 조립 후 오리지널 디자인(좌)과 디자인 변경(우)의 응력 변화 비교
결론
Moldex3D와 LS-DYNA의 결합을 통해 제품의 휨 상황을 정확하게 예측할 수 있다. Moldex3D FEA인터페이스 모듈은 섬유 배향, 열적-기계적 성질, 잔류 응력 등 분석 자료를 LS-DYNA로 전송하고, 이를 통해 구조 분석이 사출 공정에서 발생한 재료 속성 변화를 완벽하게 고려할 수 있게 하여 더욱 믿을 만한 분석결과를 얻게 된다. 라이트온 테크놀로지는 비용과 효율을 모두 고려하여 고품질 제품을 생산하고, 플라스틱 제품 설계 및 제조에 더 큰 자신감을 가질 수 있게 되었다.