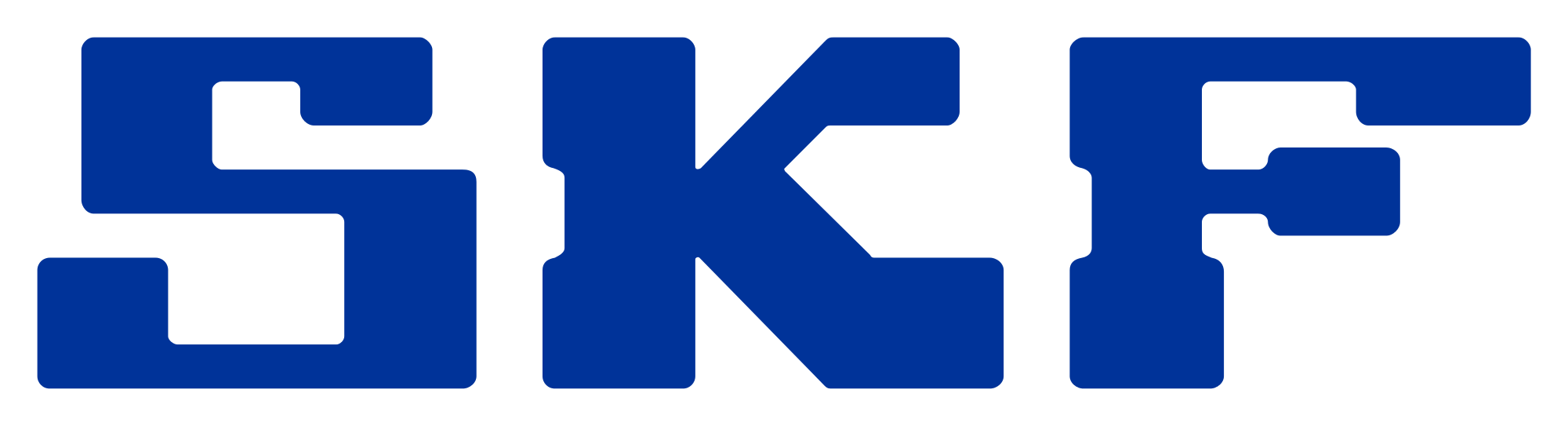
- 고객: SKF Technologies India Pvt Ltd.
- 국가: 인도
- 산업: 전자
- 솔루션: Moldex3D Advanced
(출처: https://www.skf.com/in/our-company/index.html)
개요
각 산업별로 고유의 도전과제가 있지만, 공통된 목표는 기계의 생산 시간 단축으로 인한 관리비용 절감, 안전성 향상, 에너지를 절약 및 이에 따른 비용 절감에 있을 것이다. 주요 산업 설비의 제조업체이자 엔드 유저의 기술 파트너인 SKF는 다양한 영역에 걸쳐 수십 년 동안 축적해 온 전문적인 지식을 바탕으로, 단순한 제품 공급을 넘어서는 종합 솔루션 제공을 통해 고객의 목표 달성을 돕고 있다.
본 사례 중의 SKF 센서용 전자 부품은 액체의 투입 및 기체를 보호를 위해 반드시 적합한 밀봉 과정이 필요했고, 그 방식으로 임베드먼트 또는 몰딩 성형 등을 사용했다. SKF는 Moldex3D를 사용해 전자 부품, 커넥터, 케이블 및 인쇄 회로 기판(Printed Circuit Board, PCB) 인서트 부품의 몰딩 성형 과정을 분석하였다.
도전
- 반복적인 설계 변경 및 디자인 횟수 감소
- 시뮬레이션 및 실제 테스트 몰딩 결과 비교로 결함을 발견하고 제품을 개선
- 제품 연구개발 주기를 단축
해결안
SKF는 Moldex3D Designer를 사용해 제품의 BLM 메쉬 모형을 제작하고 시뮬레이션 분석을 진행하였다. 뿐만 아니라 Moldex3D 기술 지원팀 역시 최단 시간 내에 효과적인 솔루션을 제공함으로써 큰 도움을 주었다. SKF 제품에는 전자 부품, 케이블 및 커넥터 등 매우 다양한 부품들이 포함되어 있기 때문에, 양호한 품질의 제품을 얻는다는 것은 매우 큰 도전이었다. Moldex3D 팀이 사용을 권장한 BLM 기술을 통해 SKF는 이 목표를 달성할 수 있었다.
장점
- 제조 과정 파라미터의 개선 성공
- 결함을 찾고, 설계수정 및 제조과정 설정 상의 건의를 제공
- 시뮬레이션 결과에 근거해 제품의 품질에 영향을 미칠 수 있는 원인을 파악
사례
1단계 목표는 싱글 캐비티 성형 시뮬레이션을 실시해, 기존의 제조과정 설정이 제품 설계 및 제조과정 상에 미치는 악영향에 대해 파악하는 것이었다. 시뮬레이션 결과는 반드시 실제 제조과정의 제품과 부합해야 했다. 2단계 목표는 성형의 유동학 연구를 실시해 동일 제품 중 2개의 플라스틱 인서트 부품의 성형 가능성에 대해 파악하고, 최적의 사출 위치, 런너 및 런너 게이트 설계, 냉각수로의 크기 등을 찾아내는 것이었다. 그리고 동시에1단계에서 찾아낸 제품의 결함은 반드시 이 단계에서 수정이 완료되어야 했다.
SKF 기술 센터는 Moldex3D Advanced 솔루션을 사용해 원본 설계의 성형 조건을 시뮬레이션 하였다. 먼저 소형 전자 부품 및 캐비티의 BLM 메쉬 모형을 제작한 후, Moldex3D 시뮬레이션 결과를 통해 런너 게이트의 위치가 일부 구간의 충진 문제 뿐 아니라 벽이 얇은 구간에서는 유동 지체 현상을 유발하고 있음을 발견했다. 동시에, 성형 과정 중 전자 부품 내부에 응력이 잔류하고 있음도 알 수 발견했다. SKF는 이상의 결과를 바탕으로 제조 과정 파라미터를 개선하고, 가장 낮은 성형 압력을 사용함으로써 최적화된 생산 주기를 구현할 수 있었다.
2단계의 이중 캐비티 설계에서는 런너 게이트의 형태와 위치를 변경하였고, 1단계에서 발견된 결함에 근거해 런너 시스템의 사이즈 및 설계를 변경하였다. 많은 종류의 변경이 이루어진 시뮬레이션 결과를 통해 가장 이상적인 설계를 찾을 수 있었으며, 원본 설계와 비교했을 때 변경 후의 설계가 유동을 더욱 순탄하게 만들고 지체 현상을 제거(그림 1)하였을 뿐만 아니라, 온도, 압력 및 열잔류응력 역시 순탄하게 제어할 수 있음을 발견하였다. 제조 과정의 개선을 통해 최적화된 생산 주기를 구현하고, 이를 통해 비용과 성형 압력을 낮출 수 있었다.
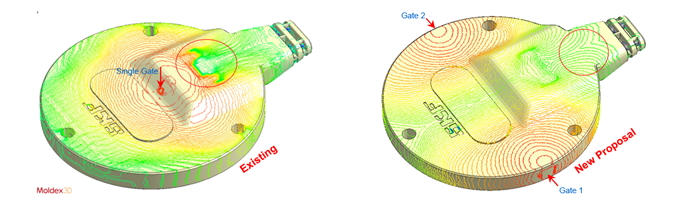
그림 1 원본 설계(좌측)의 유동 분포가 균일하지 못하며, 커넥터 등의 일부 구간에서 유동의 지체 현상이 나타남을
확인할 수 있다. 두 개의 런너 게이트(우측)로 설계를 변경한 후에는 유동이 비교적 균일하며,
지체 현상 역시 거의 모두 사라졌음을 확인할 수 있다.
SKF는 Moldex3D를 사용해 원본 설계를 시뮬레이션하고, 관찰된 결과에 따라 제조과정 및 설계변경 작업을 진행하였다. 동시에 실제 제조과정을 통해 원본 설계의 시뮬레이션 결과가 실제 상황과 상당 부분 일치함(그림 2)을 확인할 수 있었다. 설계 변경 후 Moldex3D 분석 결과를 통해 원본 설계의 문제를 개선하였을 뿐 아니라, 생산 주기 역시 단축시키고 제조 비용을 낮추었음을 확인하였다. 실제 테스트 사출 결과 역시 시뮬레이션 결과와 일치하였다.
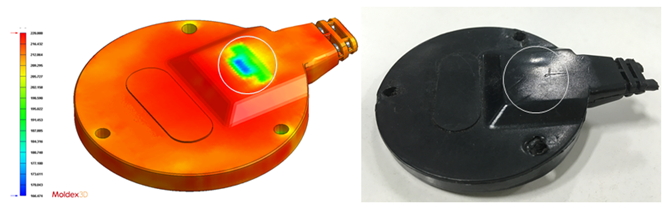
그림 2 원본 설계의 시뮬레이션 결과를 통해 움푹 들어간 흔적(좌측)을 발견하였으며, 제품 디자인 결과를 통해서도 동일한 현상(우측)을 발견함으로써, 양자가 상당히 일치함을 확인할 수 있었다.
결론
Moldex3D의 분석을 통해 SKF는 디자인 및 제조 전에 제조 과정 파라미터가 유동에 미치는 영향에 대해 완벽히 파악할 수 있었으며, 이를 통해 잠재된 결함을 예측하여 상당한 정도의 제품 연구개발 주기를 단축할 수 있었다. Moldex3D가 제공한 모든 분석 데이터는 실제 실험을 통해서 그 정확성이 입증되었다. SKF 기술 센터는 이를 통해 제조과정 파라미터를 개선함으로써 제품 결함을 유발할 수 있는 원인을 찾아 복구할 수 있었다.