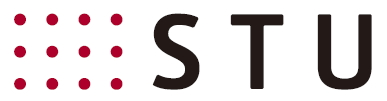
- 고객: 슬로바키아 과학기술대학교 재료과학 및 기술대학
- 국가: 슬로바키아
- 산업: 교육
- 솔루션: Moldex3D Advanced, 유동 분석 모듈 Flow, 보압 모듈 Pack, 냉각 분석 모듈 Cool, 변형 분석 모듈 Warp, 가스 보조 사출성형 모듈 GAIM
개요
본 사례에서 Moldex3D는 가스 보조 사출성형(GAIM) 제품의 뒤틀림 결함을 개선하기 위해 사용되었다. 해당 제품은 원래 전통 사출성형 프로세스로 제조된 자동차 백미러의 부품이다. 그러나 제품 중앙의 중공 구역에 심각한 변형이 발생하고 리브 구역 내부에 진공 기포가 발생하기 때문에 뒤틀림을 줄이는데 필요한 보압 시간이 종종 너무 오래 걸렸다. 따라서 STU는 GAIM 프로세스를 개선하여 결함 문제를 개선하고자 했다. Moldex3D의 시뮬레이션 결과 역시 GAIM이 뒤틀림을 효율적으로 개선하고, 성형 주기를 단축시킬 수 있다는 것을 증명했다.
도전
- 제품 중앙의 중공 구역에 큰 변형이 발생하여 후속 어셈블리에 영향을 미친다 (그림 1)
- 리브 구역 내부에 진공 기포가 발생한다 (그림 2)
그림 1 제품 중앙 중공 구역의 뒤틀림
그림 2 진공 기포 위치(a)와 체적 수축률이 높은 구역(b)
솔루션
Moldex3D사출성형(IM) 및 가스 보조 사출성형(GAIM) 모듈을 사용해 서로 다른 프로세스를 비교하고 최적화를 진행한다.
장점
- 제품 변형 원인을 성공적으로 식별하고 뒤틀림 문제를 개선
- 가스 보조 성형 프로세스의 응용 검증
- 냉각 효율 약 40% 향상
- 전체 냉각 온도 감소, 제품 수축과 진공 기포 감소
사례
본 사례의 목표는 제품의 뒤틀림을 줄이고 내부 진공 기포 문제를 제거하는 것이다. STU는 Moldex3D IM 모듈 시뮬레이션을 사용해서 제품 결함을 일으킨 근본적 원인을 찾아낸다. Moldex3D GAIM 모듈 역시 새로 도입되는 가스 보조 프로세스가 효율적으로 문제를 해결할 수 있는지 평가한다.
먼저 STU는 원래 제품 설계의 Moldex3D사출성형 시뮬레이션과 몰드 테스트 결과를 비교해 두 개가 일치하는지 확인했다. 소프트웨어는 뒤틀림 경향 및 소프트웨어가 시뮬레이션한 내부 진공 기포 위치가 실제 제품의 체적 수축이 높은 구역과 일치하는지 정확하게 예측하고, 시뮬레이션 분석에 근거하여 제품의 두꺼운 리브 위치의 열 축적 현상이 위의 제품 결함을 일으키는 주요 원인인지 표시했다.
열 축적 현상을 제거하기 위해 STU는 냉각 채널과 격판을 추가시키는 방법을 사용해 고냉각 효율을 향상시키고자 했지만, 이 방법은 예상 효과를 충족시키지 못했다. STU는 다시 보압 시간을 연장시키는 방식으로 제품 수축을 감소시켰지만 보압 시간이 불합리한 상황까지 연장되어야만 결함을 제거할 수 있었다. 따라서 STU는 가스 보조 성형 프로세스를 도입하고, 서로 다른 게이트 위치, 가스 주입구 위치 등을 포함하는 여러가지 설계 변형을 제시함으로써 비록 리브 위치에 정확하게 중공이 있다 하더라도 (그림 3) 냉각 온도를 대폭 낮출 수 있었다 (그림 4). Moldex3D 시뮬레이션 결과, 가스 보조 성형 프로세스가 개선된 후 제품의 뒤틀림과 체적 수축이 모두 감소되었고 (그림 5), 냉각 시간도 효율적으로 단축된 것으로 나타난다. 이처럼 STU는 Moldex3D를 통해 서로 다른 모듈 설계와 프로세스 매개변수를 비교함으로써 최상의 결과를 얻을 있다는 것을 알 수 있었다.
그림 3 가스 보조 성형 게이트 위치 설계 결과 비교 : (a) 처음 설계 불량 중공 발생, (b) 마지막 설계 비교적 우수한 중공 발생.
그림 4 전통 사출성형(CIM)과 가스 보조 프로세스(GAIM)의 냉각 온도 비교
그림 5 STU가 진행한 여러가지 설계 변경 중에서 원래의 CIM 제품 변형량이 가장 크고, 가스 보조 성형 제품의 기하학적 정확도가 가장 높다. 녹색 구역 : 원래 CAD모델, 빨간색 구역 : CIM 변형 모델, 보라색 구역 : 가스 보조 성형 모델.
결론
Moldex3D분석을 통해 STU는 제품 결함을 정확하게 예측하고 발생 원인을 찾아내며, 동시에 Moldex3D를 통해 프로세스 조건, 제품과 몰드 설계를 간편하게 최적화할 수 있었기 때문에 최상의 설계를 달성하기 위해 몰드를 반복 테스트하고 수정할 필요가 없었다. 또한, Moldex3D는 고급 성형 프로세스 분석 모듈을 많이 제공하기 때문에, 전통 사출성형과 서로 다른 프로세스의 결과를 비교할 수 있고, 이에 따라 STU는 불필요한 시간과 제조 비용을 낭비할 필요 없이 Moldex3D를 통해 가장 적합한 가스 보조 프로세스 설계를 찾아내서 원래 설계의 문제를 성공적으로 해결할 수 있었다.