- 고객: Taiwan University of Science and Technology
- 구역: 대만
- 산업: 교육
- 솔루션: Moldex3D Advanced / Injection Compression / Optics / Viscoelasticity
수행 요약
광학 제품의 고정밀 사출 성형에 대한 수요가 증가하고 있다. 그러나, 엄격한 광학 요구 조건 때문에 잔류 응력, 변형, 싱크 마크 문제를 방지하는 것이 중요하다. NTUST의 정밀 제조 실험실 (PML)은 위에 언급한 광학 과제를 해결하고 사출 성형 공정을 최적화 하는 In-Mold Micro Compression (IMMC)을 개발하는 것을 목표로 하고 있다. 그들은 IMMC 공정의 효과와 영향을 평가하고 시뮬레이션 하기 위해 Moldex3D 사출 압축 솔루션을 사용하였다. 시뮬레이션 결과에 따르면, IMMC 공정은 싱크 마크와 체적 수축을 크게 감소시킬 수 있으며, 집광 효율을 높일 수 있다. 이와 같은 경우 Moldex3D는 시뮬레이션 결과와 실제 성형된 제품 사이의 좋은 연관성을 제공할 수 있다고 입증하였다.
도전 과제
- 균일하지 않은 압력 분포
- 높은 수축률
- 변형
해결책
IMMC 공정의 효과를 확인하고 평가하기 위해 Moldex3D 사출 압축 시뮬레이션을 사용한다.
이점
- 균일한 압력 분포를 구한다.
- 7.35% 만큼의 휘도를 향상시킨다.
- 체적 수축을 6.62%에서 4.25%로 줄인다.
사례연구
그림. 1 프리즘 배열은 태양열을 수집하기 위해 설계된 플라스틱 광학 부품이다.
이 사례에서, PML 실험실은 프리즘 배열들의 성능을 향상시키기 위해 IMMC를 사용할 수 있는 가능성을 조사하기 위해 노력하였다. 프리즘 배열은 태양열을 수집하기 위해 설계된 플라스틱 광학 부품이다. 구조 때문에 게이트의 위치가 얇은 벽면 지역에 위치하게 되어 그 결과 나타난 유동 불균형과 높은 체적 수축은 태양열 수집, 이동, 방출과 같은 문제를 발생시킨다. 잔류 응력과 체적 수축을 감소시키기 위해 PML 실험실은 최적의 성형 공정을 결정하는데 도움을 주는 Moldex3D 성형 시뮬레이션 소프트웨어를 사용하기로 결정하였다.
그림. 2 광학 제품은 유동 불균형의 결과 두 개의 찌그러진 자국이 있다.
우선, PML 실험실은 기존의 사출 성형 공정을 Moldex3D로 시뮬레이션 하였다. 해석 결과는 싱크 마크 지수가 더 두꺼운 영역에 나타나는 것을 보여줬다. (그림. 3-좌측) 용융 온도가 높기 때문에, 싱크 마크가 발생하며, 표면은 안쪽으로 당겨진다. 싱크 마크 시뮬레이션 결과는 또한 수축이 일어날 가능성이 높은 부위가 제품의 끝부분에 발생할 거라고 나타낸다. (그림. 3)
그림. 3 보압 단계에서 싱크 마크 지수(왼쪽)와 싱크 마크 변위(오른쪽)
사출 성형공정을 시뮬레이션 한 후, 그 실험실은 Moldex3D를 제품을 최적화하기 위해 새로운 공정인 IMMC를 사용하기 위한 방법으로 테스트 하였다. 시뮬레이선 해석 결과에 의하면, IMMC의 최대 최적 수축은 일반 사출성형에 비교하여 18.9%만큼 줄어들었다. (그림. 4) 변형 문제에서, IMMC는 Z 변위를 71%만큼 개선하였다.
(b)
그림.4 보압 해석 결과는 최대 체적 수축 결과를 보여준다. (a) 사출성형 제품은 -2.9%~2.323% ,
(b) IMMC 제품은 -3.7%~0.69%
(a)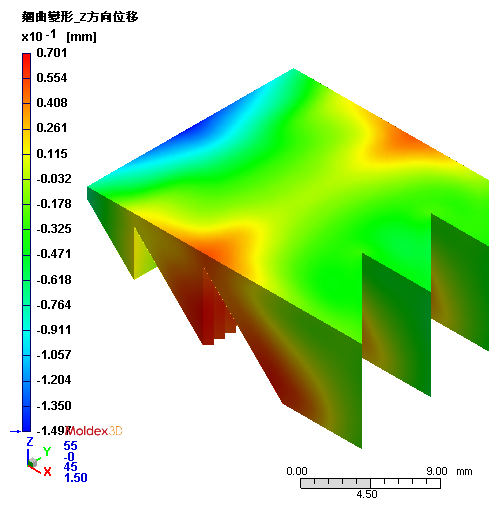
(b)
그림 5. 변형 해석은 Z 방향 변위를 나타낸다. (a) 사출성형 제품은 -1.497~0.701mm, (b) IMMC 제품은 -0.325~0.311mm
Moldex3D로 두 개 서로 다른 사출 공정의 Total Fringed Pattern을 비교하면, 사출 성형 공정의 제품에서 더욱 명확하게 Fringed Pattern이 게이트 근처에서 발견되었다. 이 분석은 사출 성형된 광학 부품은 높은 압력에 의해 큰 잔류 응력이 나타난다는 것을 보여준다. 그러나, IMMC 제품은 in-mold compression이 게이트 근처에 더 낮은 압력이 나오게 도와줄 수 있기 때문에 Fringed Pattern은 분명히 더 적게 나온다.
Fringed Pattern : 제품에 황색광을 투과 시킨 후 편광 필름을 통해 바라본 무늬.
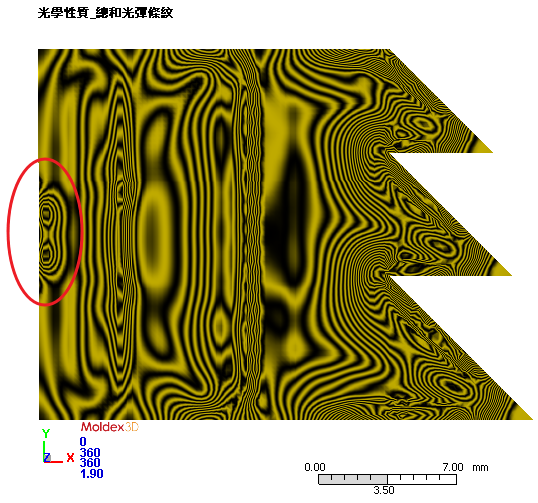
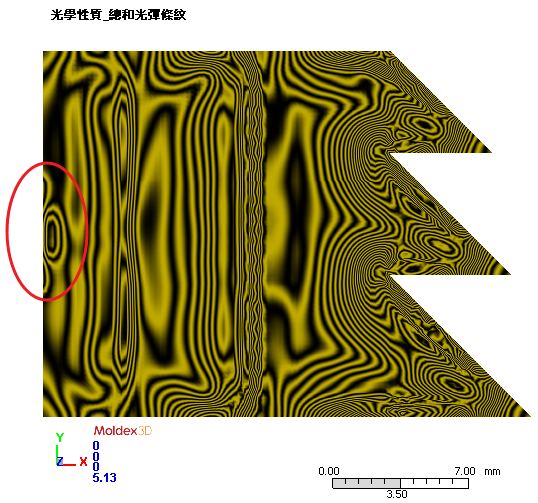
그림. 6 사출 성형(좌) 과 IMMC 공정(우)의 Total Fringed Pattern 분석 결과
PML 실험실은 시뮬레이션 해석의 사용을 검증하기 위해 실제 성형된 제품과 시뮬레이션 예측 결과의 상관관계를 연구하였다. 싱크 마크 분석 결과는 싱크 마크가 발생할 것이라고 예상되는 부분과 실제 실험 결과와 완벽하게 일치하였다. (그림. 7) 또한, IMMC 시뮬레이션 결과는 실제 실험 결과를 검증하였다. 그림. 8은 IMMC 공정이 싱크 마크를 제거하고 결함 없는 광학 제품을 생산할 수 있다고 보여준다.
그림. 7 Moldex3D의 싱크 마크 해석 결과는 실제 제품과 일치하였다.
그림. 8 IMMC 공정에 의한 제품은 큰 결함이 없다.
결론
실험실은 제품을 더 확인하기 위해 LED light를 사용하였다. IMMC와 사출 성형 공정의 제품 평균 휘도는 299Lux와 321Lux 이다. 조명은 7.35% 향상되었다. 마지막으로, 실험실은 두 공정의 Fringed Pattern 결과를 확인하였다. 그림. 9 는 시뮬레이션 결과와 실제 제품의 시험에서 fringed 패턴 결과 우수한 일치 관계를 보여준다. 시뮬레이션 결과는 실제 제품과 잘 일치하며, Moldex3D 시뮬레이션 솔루션은 광학 부품의 성형 공정에 최적화하고 효과적으로 시뮬레이션 할 수 있도록 도와준다. 또한, Moldex3D 시뮬레이션 솔루션을 사용하는 것은 실제 금형 테스트과 관련된 비용과 위험을 줄일 수 있다.