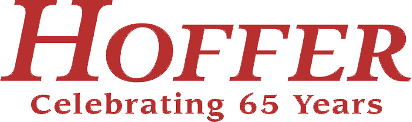
호퍼 플라스틱은 가족소유의 사출성형 전문회사로서 1953년 로버트 A와 헬렌 C 호퍼에 의하여 설립되었다. 지난 59년동안, 호퍼플라스틱은 85톤에서 600톤에 이르는 103여 사출기를 운영할 정도로 성장해왔으며, 일리노이스의 남 엘진에 36만5천 평방피트의 시설을 갖추고 있다. 국내 시설외에도, 북미 및 아시아 지역에 인텍 그룹의 운영에도 적지 않은 소유권을 가지고 있어서, 전세계 6개 시설에서 제조할 수 있는 능력을 보유하고 있다. 호퍼플라스틱의 전문영역은 주로 MuCell®, 가스주입성형, 인몰드 라벨링, 인서트성형 및 이중사출(2종재질)성형 등 으로 관련 여타 요구사항을 완결하는데 꼭 필요한 2차공정을 갖는 공정들이다. 동사는 또한 자사내 3개의 금형실을 갖추고 모든 금형기구 요구사항을 지원할 27명의 정규직 금형제작공을 운영하고 있다.(www.hofferplastics.com/)
사례
접시형 와셔 필터는 현재 시장에 출시되어 있다. 두 재료가 변형과 충진면에서 평가되었다. 이전 설계에서는 구멍들이 한 측면에서 원형 코어빼기 되었었다. 동사의 스피커 그릴의 경험과 제조설계 특허기술을 바탕으로 사각형 구멍을 활용키로 하였다. 필터는 조립시나 자체 기능으로나 평면을 유지해야만 하며, 물이 82도C(180도F) 까지 고온에 이르는 운전 시에도 인몰드 잔류응력은 조금도 허용이 되지 않았다 . 이 때문에 유동해석과 변형해석은 금형설계와 공동연계하여 수행되어야 하였고, 냉각라인모델도 정확하고 정교한 결과를 얻기위하여 Moldex3D로 보내져야 만 하였다.
그릴류 구조물의 시뮬레이션은 항상 사출시뮬레이션에서는 하나의 도전이다. 전통적 접근방식으로 그릴은 라인요소로 모델을 만들어야 하는데 매우 지루하고 충분히 정확한 결과도 얻을 수 없다. 반면, Moldex3D의 덕분으로 모델을 직접 CAD에서 가져와 자동으로 메쉬를 생성하였고, 모든 계산은 Moldex3D 설계 프로그램내 최등급 메쉬로 수행되었다. 모델이 매우 커서, STL파일이 47.5 MB나 되었다. 유동해석은 5등급메쉬로 하고, 듀얼 쿼드CPU에 16GB 램이 장착된 워크스테이션에서 수행되었다.
후 성형변형을 최소로 할 수 있는 최대의 제품충진을 얻고자 하였으며, 이를 위해 최적의 게이트 수와 위치를 결정하고자 다중으로 해석을 수행하였다. 유동해석은 4개 게이트구성과 7개 게이트구성으로 수행되었다.
실제 결과
초기 프로토타입 금형이 4게이트구성으로 제작되어 유동해석결과와 비교 확증하였다. 다음에 7 게이트구성으로 개조하여 더 나은 유동과 변형 예측을 확인코자 하였다. 주지한 바와 같이, 1.5mm로 예측된 해석결과는 실제와 매우 근접하였다. 이 변형은 몇차례의 제품교정을 통해 제품공차 범위내로 감소되었다.
아래그림은 실 사출품과 해석결과의 비교를 나타낸다.
Filling time at 32%
Filling time at 39%
Filling time at 50%
Filling time at 99%
아래그림은 4게이트경우와 7게이트경우, 유동선단시간(melt font time), 압력 및 전단응력 해석 비교를 나타낸다: