코어테크 기술지원처
- 고객: 라이트 온 테크놀러지 유한회사
- 산업: 클라우드 컴퓨팅, 자동차 전자장치, 광전자, LED 조명, 스마트 헬스케어, 정보통신, 산업 및 가전제품 등 분야에 광범위하게 적용되는 광전 소자 및 핵심 전자 모듈
- 솔루션: Flow
1975년에 설립된 라이트 온은 「광전자 에너지 절약, 스마트 기술 분야 최적의 파트너」를 비전으로 핵심 광전 소자 및 핵심 전자 부품 발전에 포커스를 둔 업체로, 자원 통합 및 관리 최적화를 통한 양산 이점을 구축에 힘쓰고 있습니다. 라이트 온은 컴퓨터, 통신, 가전제품, 자동차 전자장치, LED 조명, 클라우드 컴퓨팅 및 의료 등의 분야에 널리 적용되는 제품을 제공하며, 그중 광전자 제품, 정보통신기술, 저장장치 등은 모두 세계 시장을 선도하고 있습니다.
40여 년 동안 양산 방면에서 경쟁적 우위를 확보하는 데 전념해 온 라이트 온은 다양한 제품 포트폴리오의 효율성을 최적화하는 자원 통합 및 관리를 통해 고품질의 매출 성장 및 수익성을 달성해 왔습니다. 최근 라이트 온은 정보통신산업에서 클라우드 컴퓨팅, LED 조명, 자동차 전자장치, 지능형 제조, 5G+AIoT 등의 분야로 적극 전환하여 라이트 온의 새로운 운영 성장 모멘텀을 창출하였습니다. 라이트 온은 큰 변화와 도전의 시대에 세계적 수준으로 우수한 기업의 기존 이점을 지속적으로 활용함으로써, 광전자 에너지 절약 및 스마트 기술의 혁신 및 응용을 추구하는 글로벌 고객이 가장 선호하는 최고의 비즈니스 파트너가 될 것으로 기대됩니다.
개요
라이트 온은 Moldex3D를 통해 다양한 재료 및 크기의 몰드 캐비티를 통합하고, 핫러너와 콜드 러너의 구성을 기획하고 웰드 라인을 최적화하였습니다. 라이트 온은 먼저 문제를 분석하고 검증하여 제품 및 몰드 캐비티의 실행 가능성을 평가했습니다. 이를 통해 전통적인 시행착오 방법을 피하고, 자동화 팀의 지원 및 통합을 통해 사출 후 제품 자동 적층 등의 작업을 실현함에 따라 후반 조립에 필요한 인력을 줄였습니다.
도전
이제 다양한 크기의 제품이 몰드를 공유하려면 유동 불균형, 외관 게이트 응력 표시, 대형 버튼의 웰드 라인, 제품 크기 차이 및 변형 문제를 해결해야 합니다.
솔루션
- Moldex3D Designer BLM은 솔리드 메쉬 레이어에서 전단 가열을 효과적으로 평가할 수 있습니다.
- Moldex3D를 적용하여 러너 직경, 구성 및 생산에 필요한 재료 온도, 몰드 온도를 정확하게 제어할 수 있습니다.
효과
- 제품 및 몰드 설계의 실행가능성 평가
- 유동 불균형 문제 해결
- 외관의 웰드 라인 문제 해결
사례 연구
현재 노트북 키보드의 키 레이아웃은 US, UK, BZ, JP 등 4가지 언어군으로 구분될 수 있습니다. HP를 예로 들면, 빨간색으로 표시된 부분은 각 언어의 키 레이아웃이 다른 부분입니다. 따라서 모델의 개발에 있어 다양한 크기의 버튼은 다양한 캐비티 수를 갖는 다양한 몰드 세트를 필요로 합니다. 이렇게 되면 몰드 상의 관리가 불편해지고, 상부 다이, 셧 다이, 하부 다이, 다이 교체를 빈번하게 수행할 많은 인력이 필요합니다.
또한 이후의 수작업 조립에서도 하나씩 눌러서 조립해야 하는 많은 인력이 필요하므로 비용 측면에서 효율적이지 않습니다. 따라서 패밀리금형(family mold) 사출 성형과 자동화 조립을 통합하여 인력과 기계 비용을 절감해야 합니다.
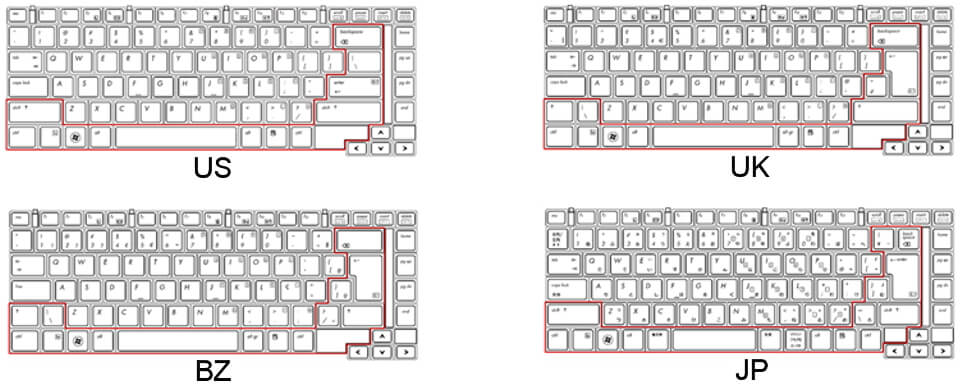
그림 1 언어군에 따른 키보드 크기 차이(빨간색 표시)
패밀리금형(family mold)는 전단 가열로 인한 유동 불균형을 정확하게 고려해야 하고, 고객이 다양한 재료를 사용해 생산하도록 요구하기 때문에 이러한 문제를 해결하기 위해 시뮬레이션 분석은 반드시 필요한 부분입니다. 시뮬레이션 분석은 실제 테스트 시에 발생하는 비용을 절감할 뿐 아니라 문제 개선을 위한 설계 변경 검증을 구현할 수 있으므로 몰드 개발 및 테스트 비용을 크게 줄일 수 있습니다.
이번 연구에서는 Moldex3D를 통해 설계자와 제조업체가 동일한 패밀리금형에 다양한 재료를 적용할 수 있는지 타당성을 평가할 수 있도록 다양한 재료의 유동 상황을 예측합니다. Moldex3D Designer BLM은 유동 불균형, 웰드 라인 문제와 같이 성형에서 발생할 수 있는 문제를 방지할 수 있도록 솔리드 메쉬 레이어에서 전단 가열을 효과적으로 평가하며, 러너 직경, 구성을 정확하게 제어하고 생산에 필요한 재료 온도, 몰드 온도 등을 정확하게 예측합니다.
먼저, 서로 다른 재료가 동일한 패밀리금형에 적용할 수 있는지에 대한 검증을 수행하면(그림 2는 다양한 재료의 점도 대 전단율임), 4가지 재료 간의 점도 차이가 매우 크지만 서로 다른 재료에 대한 각각의 분석을 통해, 유동 거동, 사출 압력 및 형체력이 모두 비슷한 결과를 나타내므로, 이 4가지 재료는 동일한 기계, 동일한 몰드를 사용해 생산할 수 있음을 알 수 있습니다.
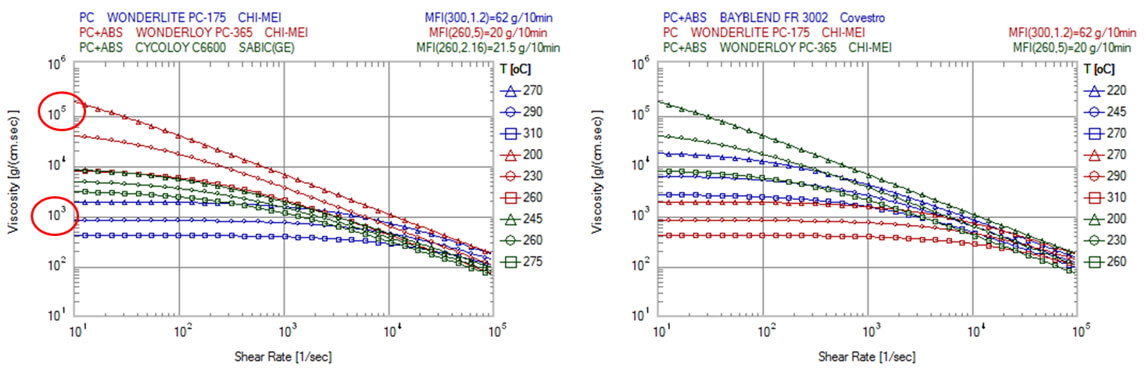
그림 2 다양한 재료의 점도 비교도
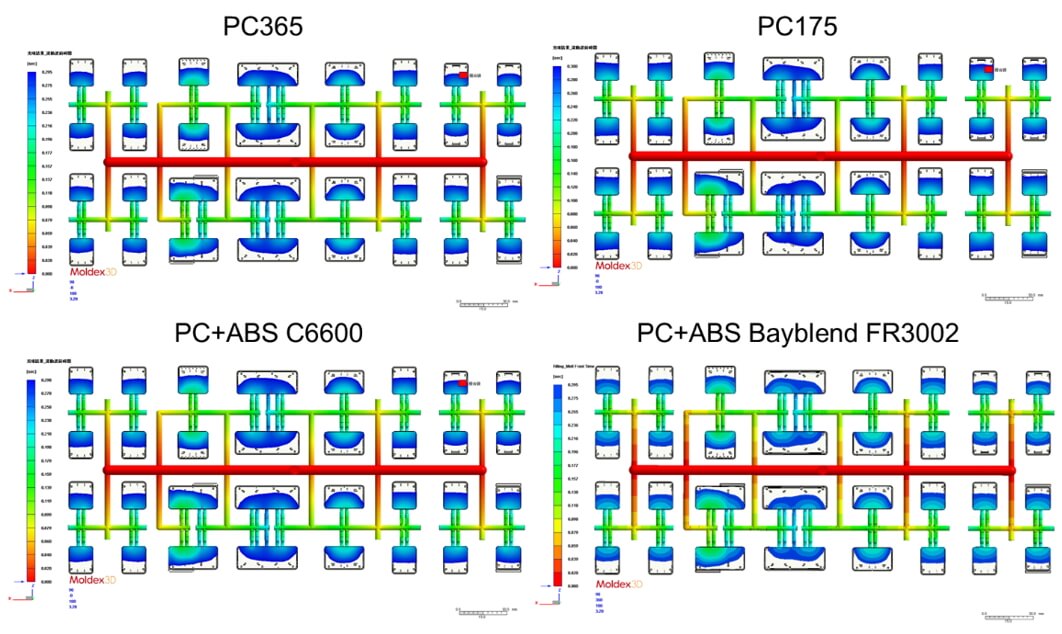
그림 3 다양한 재료의 유동 선단도(80%)
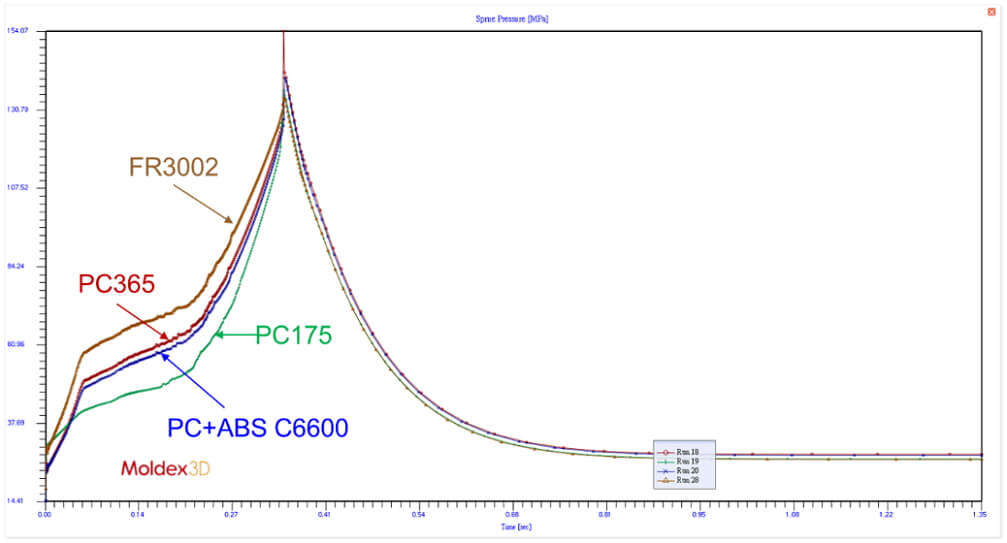
그림 4 다양한 재료의 게이트 압력 곡선도
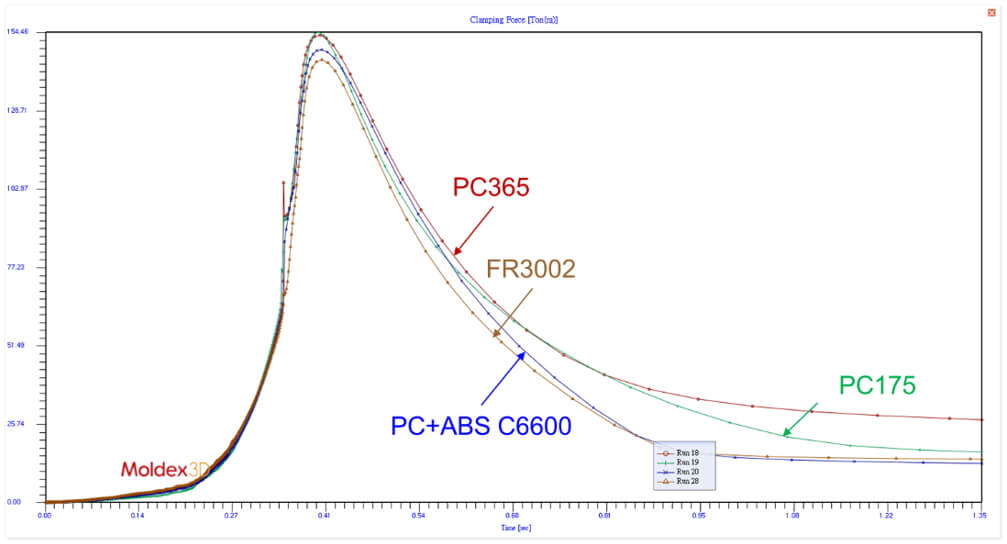
그림 5 다양한 재료의 형체력 곡선도
이어서 패밀리금형(family mold)에 대한 유동 균형 분석을 수행합니다. 업계에서는 패밀리금형의 러너를 설계할 때 일반적으로 일자형 러너 및 이중 게이트 설계를 사용하지만(그림 6), 이 두 설계는 유동 불균형 및 유동 정체 문제를 야기합니다. 따라서 Moldex3D 분석을 통해 러너 크기, 게이트 위치, 게이트 수량을 제때에 변경하여 유동 균형 설계를 달성해야 합니다(그림 7은 원래 설계이고, 그림 8은 최적화 설계이며, 가려진 부분은 기밀로 비공개 부분임). 원래 설계에서 충전 비율이 42%이면 첫 번째 줄의 작은 캐비티는 충전이 되지만 나머지 캐비티는 채워지지 않기 때문에 일부 캐비티에서 지나친 보압으로 인해 플래시 등의 문제가 발생할 수 있습니다. 최적화된 설계 그룹에서 충전 비율이 70%이면 모든 캐비티가 원래 설계보다 더 균형 있는 충전 거동을 가지므로 최적화 설계가 유동 불균형 문제를 해결할 수 있음을 알 수 있습니다. 또한, 최적화 설계는 웰드 라인 수(그림 9), 전단 응력 분포(그림 10)를 개선하고, 게이트 압력(그림 11)을 낮추고 생산 시의 난이도도 줄여줍니다.
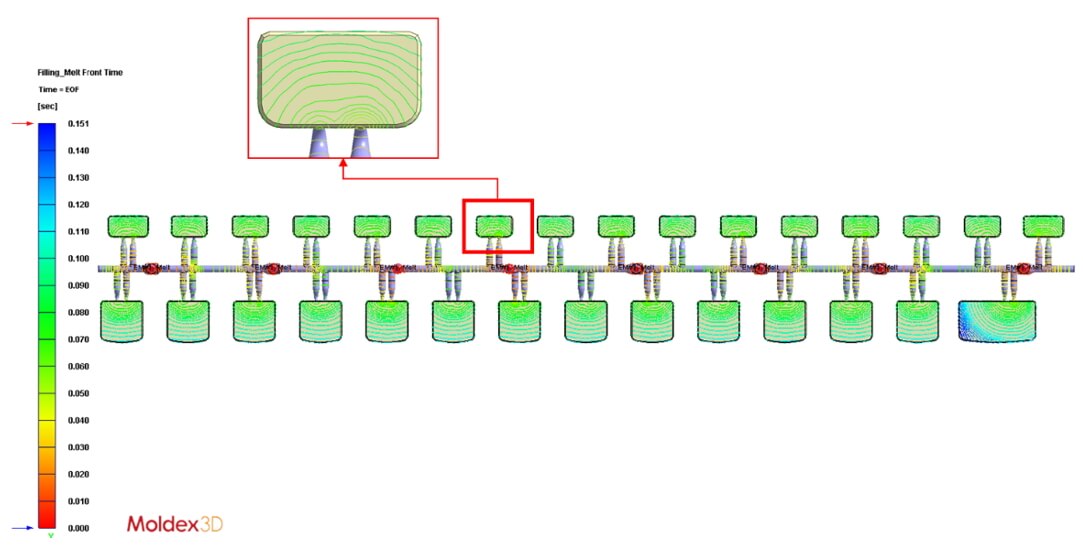
그림 6 일자형 러너 및 이중 게이트 설계
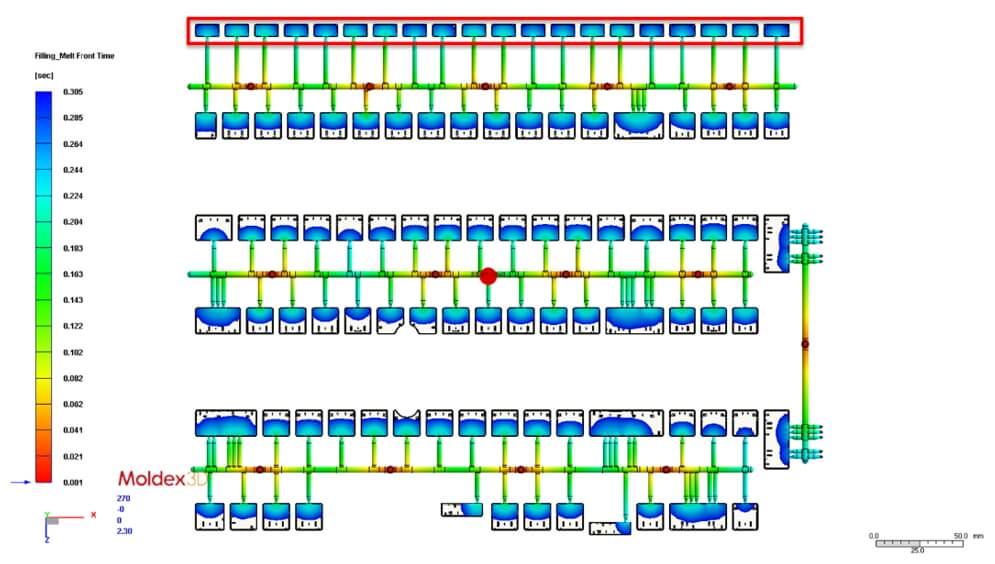
그림 7 원래 설계 (충전 비율 42%)
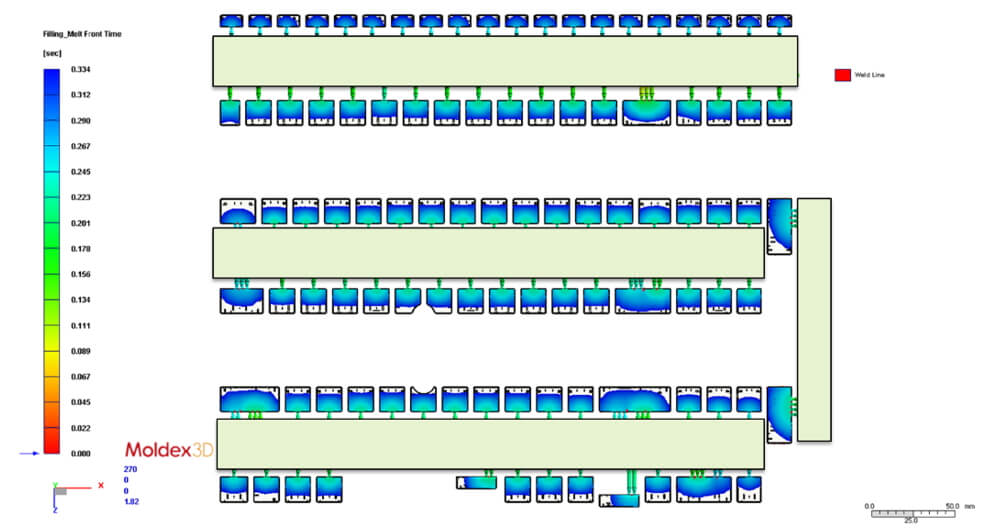
그림 8 최적화 설계(충전 비율 70%)
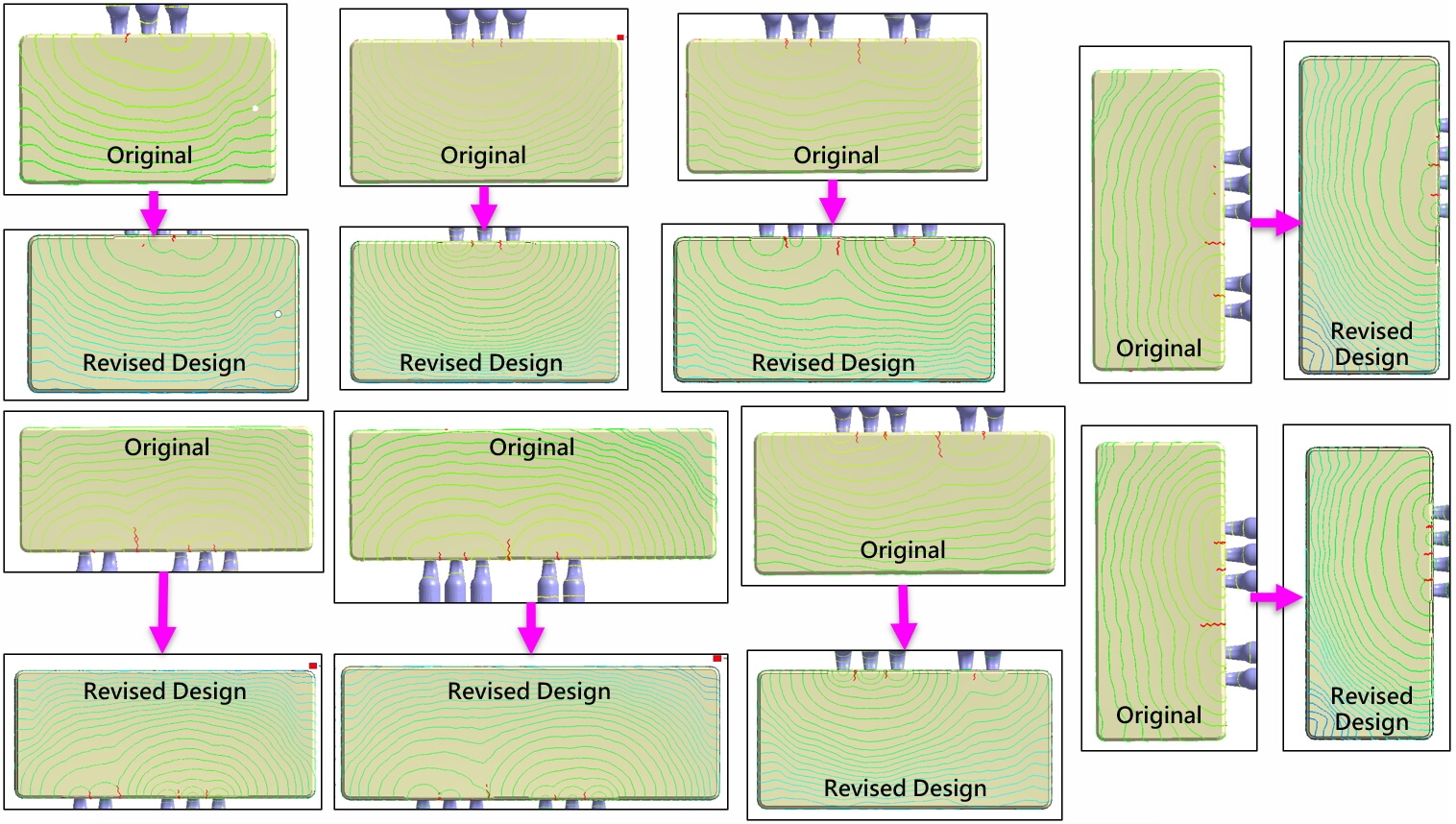
그림 9 설계 변경 전후의 웰드 라인 비교도
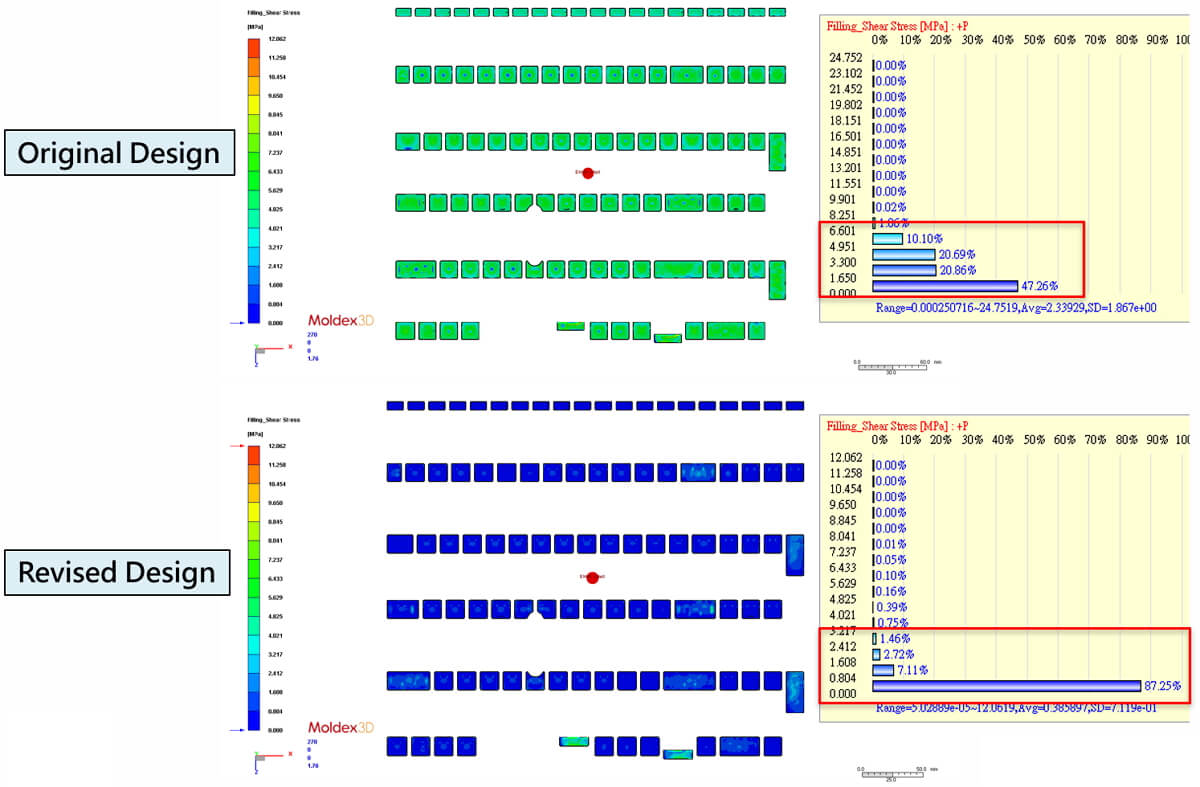
그림 10 설계 변경 전후의 전단 응력 비교도
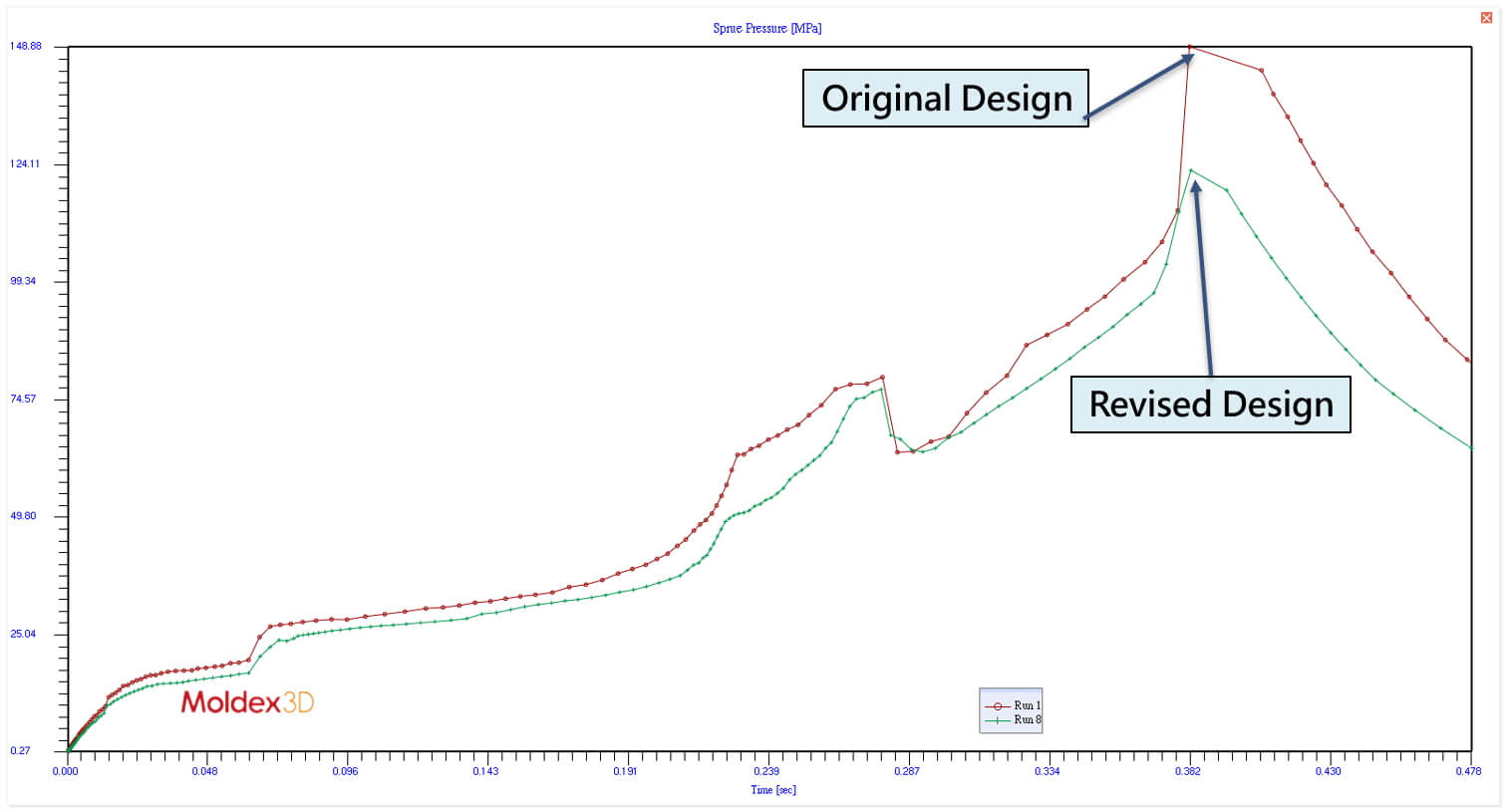
그림 11 설계 변경 전후의 게이트 압력 곡선 비교도
결과
연구 결과에 따르면, Moldex3D를 통해 콜드 러너 설계를 편리하게 수정하여 제품의 유동 균형이 효과적으로 개선되고, 전반적인 게이트 정체 문제도 효과적으로 개선되었습니다. 또한, 균일한 보압으로 플래시 문제도 효과적으로 감소되었습니다. 유동 균형의 개선으로 인해 사출 압력도 148MPa에서 120MPa 정도로 감소하여 형체력이 효과적으로 감소되는데, 이렇게 하면 원래 350톤이 필요하던 기계 톤수를 250톤까지도 줄일 수 있습니다. 또한 원래 웰드 라인이 지나치게 길어서 외관의 뚜렷한 결함 및 약한 인장강도 등의 문제도 Moldex3D를 사용해 초기 설계 단계에서 제거할 수 있으므로, 외관과 결합 강도가 개선될 수 있습니다.