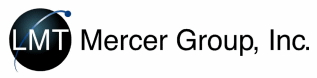
- 고객사: LMT Mercer Group, Inc.
- 국가: 미국
- 산업: 펜스 발코니 등
- 솔루션: Moldex3D eDesign
(출처: https://lmtproducts.com/)
개요
본 사례의 조명품은 2개의 부품으로 구성되고, 원재료는 동일하나 하나의 금형에서 모두 사출된다. 하지만 두 부품의 크기가 상당한 차이가 있어서, 유동 불균형 현상이 발생하였다. LMT그룹은 Moldex3D를 사용하여, 형체력 톤수의 급증 현상을 발견할 수 있었으며, 런너/게이트 및 냉각 시스템의 최적화를 통해 유동 불균형 현상과 형체력의 급증 현상을 개선할 수 있었다. 동시에 냉각 시간도 단축해, 냉각 효율성과 제품의 평평도 문제를 개선함으로써 적지 않은 시간과 비용을 절약하는 데 성공하였다.
과제
- 두 부품의 충진을 동시에 완료토록 해야 함.
- 부품의 과도한 변형(뒤틀림) 방지를 위한, 런너/게이트 및 냉각 채널의 크기와 위치를 도출함.
해결안
Moldex3D로 충진, 보압, 냉각 및 변형에 대한 분석정보를 체계적으로 제공하여, LMT설계자가 런너/게이트 및 냉각 시스템의 설계를 변경할 수 있도록 함으로써, 충진 시간, 성형 주기, 냉각 효율 및 제품의 평평도 문제를 대폭 개선토록 함.
장점
- 보압 최종단계에 필요한 형체력을 225톤에서 175톤으로 줄이는데 성공, 더 작은 크기의 프레스장비를 사용할 수 있게 되어 생산비용을 절감함.
- 두 부품 모두 정확히 1.28초에 충진 하는데 성공함. (원설계에서는 큰 부품은 1.28초, 작은 부품은 1.07초에 충진 됨).
- 최적의 냉각채널 설계를 통해 냉각 시간을 11.99% 단축하고, 냉각효율을 25.452% 에서 13.759%로 낮추는 데 성공함.
- 평평도의 경우, 작은 부품은 2.56%, 큰 부품은 6.18% 개선함.
- 금형 및 샘플 품질 관리 비용으로 약 1,200만원 이상을 절감함.
사례
본 사례는 최적화된 런너/게이트를 통해 더 작은 크기의 프레스장비의 선정과 공정 시간의 단축을 통한 비용 절감에 그 목적을 두고 있다. 또한, 성형 주기를 단축하고 제품의 평평도를 오차 허용 범위 내로 유지함으로써, 금형 공정과 시작 비용을 감소시키고자 하였다.
LMT그룹은 Moldex3D eDesign을 사용하여, 하나의 금형 안에 서로 다른 두 개의 캐비티를 설계하는 데 성공하였다. 이 중 작은 부품은 LED 보드 홀더이고, 큰 부품은 광원 반사판이다. 또한, Moldex3D를 사용해 용융선단(melt front)의 불균형 현상, 형체력의 급증, 최대 냉각시간, 과도 냉각 라인 및 두 부품의 Y축 변위 등에 대한 해석 작업을 진행하였다.
런너 레이아웃과 냉각 시스템에 적용된 설계변경 내용은 그림1, 그림2와 같다.
그림1. 원설계(좌)에서는 작은 부품에는 엣지 게이트, 큰 부품에는 점프 게이트를 사용한 반면, 변경 설계(우)
에서는 큰 부품에는 점프 게이트를 그대로 유지하고, 작은 부품에는 확장된 점프 게이트를 사용함.
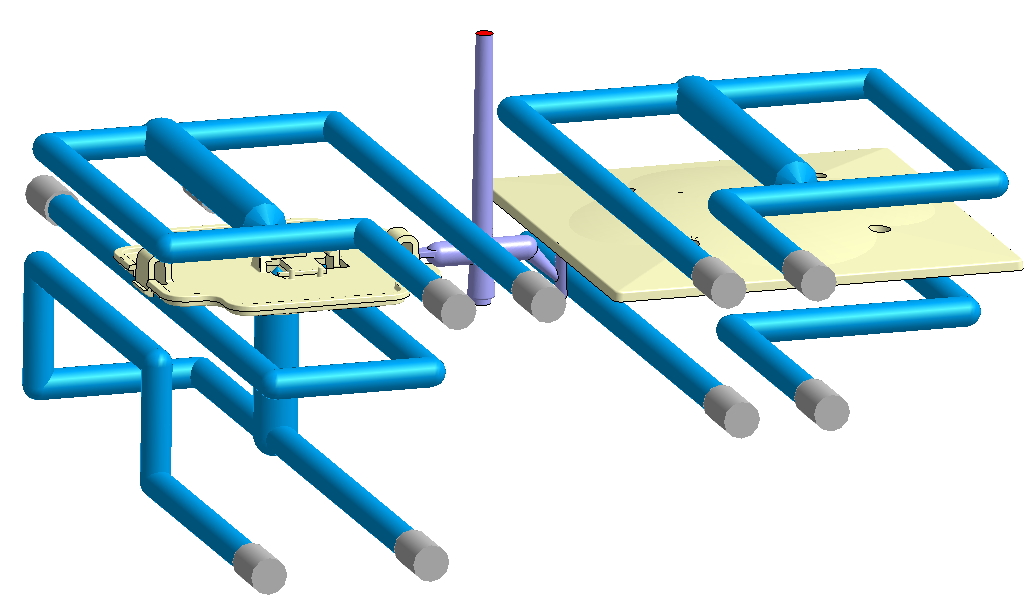

그림2. 원설계(좌측)와 달리, 변경설계(우측)는 큰 부품용 루프 냉각채널의 상.하단을 분리하고, 또한 하단에 냉각채널을 추가로 배치함.
Moldex3D로 해석한 결과에 따르면, 원설계는 작은 부품의 충진시간이 큰 부품의 충진시간보다 더 빠르다. 반면, 변경 설계는 작은 부품의 이동 경로를 길게 수정함으로써 큰 부품의 충진시간과 일치하도록 수정하였다(그림3).
그림3. 원설계(그림 상)의 74% 충진 용융선단시간과 변경설계(그림 하)의 96% 충진 용융선단시간을 비교해 보면,
두 캐비티의 불균형 충진 공정이 해결되었음을 알 수 있다.
이 밖에도, 냉각채널 시스템의 최적화를 통해 최장 냉각 시간이 기존 21.009초에서 18.489초로 단축되었을 뿐 아니라, 성형 주기 역시 단축되었고, 부품의 평평도를 의미하는 Y축 변위 수치 역시 개선되었다. 원설계에서의 변형이 큰 부품과 작은 부품 각각 0.6985mm, 0.1981mm이었으나, 변경설계에서는 각각 0.6561mm, 0.1930mm으로 개선되었다.
그림4. 큰 부품과 작은 부품의 Y축 변위 해석 결과에서 보듯이, 원설계(좌측)의 변위량이 변경 설계(우측)의 변위량 보다 더 크다.
설계 변경의 결과는 실 사출품을 통해서도 확인할 수 있었다. 공정엔지니어는 충진이 완료되기 전에 미성형이 발생함을 미리 파악할 수 있었다. 그림5에서 확인할 수 있듯이, 실 사출물과 Moldex3D의 해석 결과물이 일치함을 알 수 있다.
그림5. 설계 변경 후의 실 사출품, 크고 작은 양 부품의 미성형 모두 해석결과와 일치함.
결론
본 사례는 생산 비용의 절감과 제품 품질의 개선이라는 두 가지 목적을 동시에 달성하였으며, 금형소재가 가공되고 형상화 되기 이전에 런너/게이트 설계의 변경과 냉각 시스템의 최적화 작업을 이룰 수 있었다. 사용자는 Moldex3D를 통해 다양한 설계검토 작업과 가상시험을 쉽게 진행할 수 있어 제조 후 값비싼 재설계 재 작업을 회피할 수 있었다. 또한 금형과 부품의 설계를 개선함으로써 금형 샘플제작이나 시장출시를 제때에 이행 수 있었다. 이로 인해 상당한 제조시간과 비용절감을 성취할 수 있었다. 더구나, 실 사출품과 해석결과를 비교하여 실제 충진과 해석결과가 매우 일치하여 제조 전 선 검증할 수 있었다.