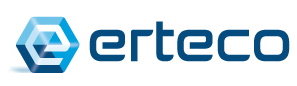
- 고객 : Erteco Rubber & Plastics AB
- 국가 : 스웨덴
- 산업 : 플라스틱 소재
- 솔루션 : Moldex3D Advanced 패키지, 유동 분석 모듈 Flow, 보압 분석 모듈 Pack, 냉각 분석 모듈 Cool, 왜곡 분석 모듈 Warp, 섬유 배향 모듈 Fiber, FEA 인터페이스 기능 모듈, 다재료 사출성형 MCM
개요
본 사례에서 Erteco는 선박 프로펠러 내부 허브 부품의 크랙 현상을 일으키는 원인을 찾아내고 이를 해결하고자 한다. 선박 프로펠러는 높은 하중을 받는 상황에서는 회전 중에 크랙 현상이 발생할 가능성이 매우 높은데, 이럴 경우 제품 전체의 품질과 성능에 타격을 준다.
도전
- 큰 용량의 엔진을 사용하고 높은 부하가 걸리는 경우, 연결부 플라스틱에 크랙 현상이 발생하기 쉬움
- 금속 부품으로 강성을 보강하는 경우 고비용이 발생함
솔루션
Erteco는 Moldex3D를 사용해 “Weld line” 위치를 예측하고, 또한 새로운 솔루션을 시뮬레이션함으로써 잠재된 문제를 파악함
효과
- 제조 공정 조건 최적화
- ETT(Ems Tape Technology ) 기술을 활용해 카본 파이버 테이프의 강도를 보강함으로써 고분자 복합물과의 완벽한 결합이 가능하다는 사실을 발견
- 프로펠러의 가장 얇은 부위에 나타날 수 있는 심각한 “Weldline” 위치에서 발생하는 크랙 문제 해결
- ETT 기술로 프로펠러의 구조 보강 후 비용 절감 효과 발생
사례 연구
본 사례의 주 목표는 프로펠러 날개와 허브에 높은 부하가 걸릴 시 쉽게 파손되는 문제를 해결하는 경제적 해결 방식을 찾아내는 것이다(그림 1). 제조업체인 Propulse는 수공으로 플라스틱 인서트 재료를 기계에 삽입한 후 메탈 칼라를 고정해 구조를 강화하는 방식을 사용했다(그림 2)
그림 1 Propulse의 프로펠러 날 모형 분해도, 그림 속 동그라미로 표시된 부분이 본 사례의 메인 연구대상이다. (Propulse AB, 2015)
그림 2 본 사례의 제품은 원래 메탈칼라를 사용해 구조를 강화하였다
1차 시뮬레이션 분석 진행 시 유동 특징을 통해 심각한 “Weldline” 문제가 발생함을 발견하였다. 해당 위치는 프로펠러 날 회전 시 프로펠러 허브에 높은 가속도를 발생시켜 과도한 부하를 주는 위치와 동일했다. 해당 부위는 제품에서 가장 얇은 부위여서 “Weldline” 문제 발생 시 제품의 강도를 심각하게 저해했다.
이 문제를 개선하기 위해 Erteco는 아마이드 및 카본 파이버 합성 테이프, Ems Tape Technology(ETT)를 활용해 기존의 방식을 대체하고 Moldex3D로 해당 신기술의 유용성을 검증했다. 시뮬레이션 과정에서는 센서 노드를 사용해 사출 성형 시의 온도와 압력 변화를 모니터링했다. 1차 사출 성형 테스트를 통해 테이프와 고분자 복합물이 완벽하게 결합하지 않음을 발견했고, 이에 Erteco는 두 가지 서로 다른 조건의 시뮬레이션을 진행하였다. 하나는 기존 설정(그림 3)을 그대로 유지한 채, 다른 하나는 몰드와 재료의 온도를 높여(그림 4) 시뮬레이션을 진행했다.
그림 3 EET 시뮬레이션 사례 채택(기존 설정)
그림 4 몰드와 재료의 온도를 높인 후의 EET 시뮬레이션 사례
Moldex3D의 분석 결과에 따르면, 몰드 온도와 보압 압력을 높일 경우 제품의 수축 가능성을 낮춰 테이프가 부품 본체에서 떨어져 나가는 현상을 방지할 수 있었다. 이는 온도와 보압이 압력이 높은 환경에서는 제품 취약부 보압 단계 유동선단 온도가 접착 온도보다 높은 시간을 늘일 수 있어, 테이프와 고분자 결합물이 완벽하게 결합할 수 있는 시간을 확보할 수 있기 때문이다.
결과
Erteco의 엔지니어들은 Moldex3D를 활용해 플라스틱 부품의 품질 문제를 확인하고 단기간 내에 문제를 해결함으로써 비용적 이익을 얻을 수 있었다. Erteco는 이에 그치지 않고 지속적으로 Moldex3D로 분석을 진행함으로써 새로운 제조공정 조건을 최적화하고 제품의 품질을 개선할 수 있었다.